Cost Optimization in Production Planning
In Food and Beverage manufacturing, production planners are the unsung heroes behind the scenes. They face the daunting task of creating efficient production schedules that meet customer demands while keeping costs in check.
In this blog, we'll explore the art of cost optimization in production planning, with a special focus on how integrating PlanetTogether with leading Enterprise Resource Planning (ERP), Supply Chain Management (SCM), and Manufacturing Execution Systems (MES) can help Food and Beverage manufacturers achieve this goal.
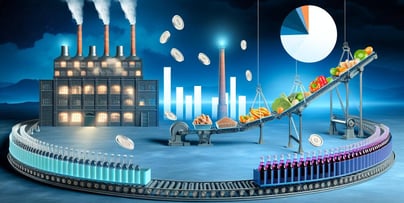
The High Stakes of Cost Optimization
Cost optimization is a top priority for Food and Beverage manufacturers. Profit margins are often razor-thin, and the competitive landscape is relentless. Here's why effective cost optimization in production planning is essential:
Maximizing Profitability: Reducing production costs directly impacts profitability. Every dollar saved in the production process goes straight to the bottom line.
Competitive Advantage: Manufacturers who can offer high-quality products at competitive prices gain an edge in the market.
Meeting Customer Expectations: Customers demand quality products at affordable prices. Effective cost optimization allows manufacturers to meet these expectations.
Resource Allocation: Efficient use of resources, such as labor, materials, and machinery, ensures that none of these critical assets go to waste.

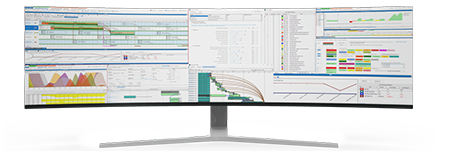
Effective Strategies for Achieving Cost Optimization in Production Planning
Data-Driven Decision-Making
The foundation of cost optimization in production planning is data. Integrating PlanetTogether with ERP systems like SAP, Oracle, or Microsoft Dynamics provides access to a wealth of data, including historical production records, inventory levels, and customer orders.
By harnessing this data, production planners can make informed decisions regarding production quantities, resource allocation, and scheduling. For instance, analyzing historical demand patterns allows for more accurate forecasting, reducing the risk of overproduction and wasted resources.
Lean Manufacturing Principles
Lean manufacturing is a set of principles and practices designed to eliminate waste and improve efficiency. Production planners can apply these principles to reduce costs:
Just-In-Time (JIT) Production: Integrate SCM systems like Kinaxis to synchronize supply chains, ensuring that materials arrive precisely when needed, minimizing excess inventory costs.
Kaizen: Continuous improvement efforts can identify and eliminate inefficiencies in the production process, reducing waste and associated costs.
5S Methodology: Organize workspaces for efficiency, reducing downtime due to searching for tools or materials.
Inventory Management
Excess inventory ties up valuable capital and increases carrying costs. Production planners can leverage ERP systems to implement effective inventory management strategies:
Safety Stock Optimization: Analyze historical demand patterns and integrate SCM systems to determine the ideal level of safety stock to avoid stockouts without excessive inventory buildup.
Inventory Turnover: Monitor and improve inventory turnover rates to reduce carrying costs.
Vendor-Managed Inventory (VMI): Collaborate with suppliers to manage inventory levels more efficiently, reducing storage costs and stockouts.
Production Scheduling Optimization
PlanetTogether's integration with MES systems like Aveva provides real-time visibility into production processes. This data can be leveraged for:
Machine Utilization: Optimize machine schedules to ensure maximum utilization, minimizing idle time and energy costs.
Batch Size Optimization: Use historical data and predictive analytics to determine the optimal batch sizes that minimize waste and maximize efficiency.
Dynamic Scheduling: Adjust production schedules in real-time to respond to changing demand or unexpected disruptions, reducing downtime and overtime costs.
Energy Efficiency
Reducing energy consumption not only lowers production costs but also aligns with sustainability goals. MES systems integrated with PlanetTogether can help monitor and optimize energy usage by:
Real-Time Monitoring: Track energy consumption in real-time to identify opportunities for reduction.
Peak Demand Management: Shift energy-intensive processes to off-peak hours when energy costs are lower.
Equipment Upgrades: Use data from MES systems to identify energy-inefficient equipment that may require upgrades or replacements.
Supplier Collaboration
Effective collaboration with suppliers can lead to cost savings. ERP systems integrated with Supplier Relationship Management (SRM) modules enable:
Negotiating Better Terms: Use data to negotiate favorable terms with suppliers, such as discounts for early payments or volume discounts.
Collaborative Forecasting: Share demand forecasts with suppliers to ensure a steady supply of materials while minimizing excess inventory.
Employee Training and Skill Development
A well-trained workforce is more efficient and less prone to errors. Integrating HR modules with ERP systems allows production planners to:
Track Training Records: Ensure that employees receive proper training and certifications, reducing errors and downtime.
Identify Skill Gaps: Analyze employee skills and identify areas where additional training is needed to improve efficiency.
Cost optimization in production planning is the linchpin of success for Food and Beverage manufacturers. Integrating PlanetTogether with leading ERP, SCM, and MES systems empowers production planners with the tools and data needed to make informed decisions and streamline operations.
By embracing data-driven decision-making, Lean manufacturing principles, efficient inventory management, production scheduling optimization, energy efficiency, supplier collaboration, and employee training, manufacturers can reduce costs, improve profitability, and maintain a competitive edge in a demanding industry.
In the Food and Beverage manufacturing landscape, cost optimization is not just a strategy; it's an imperative. With the right tools and integration, production planners can navigate the challenges and emerge as champions of cost efficiency and profitability.
Are you ready to take your manufacturing operations to the next level? Contact us today to learn more about how PlanetTogether can help you achieve your goals and drive success in your industry.
LEAVE A COMMENT