Coordinating Plant Operations in Chemical Manufacturing
From managing raw materials to ensuring timely production and maintaining strict safety and quality standards, every aspect of your operation must work in harmony. The increasing demands of modern manufacturing—greater customization, faster delivery times, and higher efficiency—mean that a coordinated, streamlined approach is more critical than ever.
In the pursuit of operational harmony, one tool that has proven transformative is the integration of PlanetTogether with leading Enterprise Resource Planning (ERP) systems like SAP, Oracle, Microsoft, Kinaxis, and Aveva. This combination offers chemical manufacturers a robust solution for seamless planning, scheduling, and production optimization across the entire value chain. Here’s how integrating PlanetTogether with your ERP can help you gain better control over your plant operations, reduce inefficiencies, and improve overall productivity.

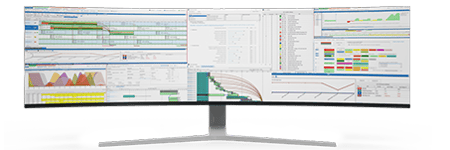
How Integrating PlanetTogether with ERP Systems can Help Gain Better Control over Plant Operations
Centralized Data Management
A major challenge in chemical manufacturing is managing vast amounts of data across multiple functions—from inventory and procurement to production and quality control. This data is often siloed in various departments, leading to communication breakdowns and bottlenecks. Integrating PlanetTogether with an ERP system like SAP or Oracle enables centralized data management, creating a single source of truth that everyone in your facility can rely on.
By consolidating data from every part of the production process, you can make more informed decisions based on real-time information. For instance, when a particular raw material is running low, your integrated system will flag it, alerting the necessary teams and automatically adjusting production schedules to avoid delays. This real-time data flow not only streamlines communication across departments but also enables proactive decision-making.
Enhanced Production Scheduling and Planning
Effective production scheduling is critical in chemical manufacturing, where certain processes may take hours, if not days, to complete. The integration of PlanetTogether with ERP systems, such as Kinaxis or Microsoft Dynamics, enables advanced production scheduling that can adapt to sudden changes in demand, resource availability, or unexpected delays.
PlanetTogether’s advanced scheduling capabilities allow you to account for variables like machine capacity, labor availability, and equipment maintenance needs. Integrating this with your ERP system ensures that everyone has access to an accurate, real-time schedule that reflects the current status of your operations. In the event of a disruption, the integrated system can automatically update the schedule, helping you avoid costly downtime and reduce waste.
In addition, predictive analytics can anticipate potential production issues, enabling you to address them before they escalate. For example, if a batch process is projected to take longer than expected, the system can adjust subsequent schedules or allocate additional resources to meet deadlines, ensuring you remain on track without compromising product quality.
Improved Inventory and Materials Management
Efficient inventory management is a major challenge in chemical manufacturing, where materials are often hazardous, perishable, or difficult to store. Integrating PlanetTogether with ERP systems like Aveva or SAP allows for real-time tracking of raw materials, work-in-progress items, and finished goods, helping you maintain optimal inventory levels and prevent stockouts or excess inventory.
This integration enables just-in-time (JIT) inventory management, where materials arrive exactly when they are needed. This minimizes storage costs, reduces waste, and improves cash flow. Additionally, automated alerts for low inventory levels, upcoming expiration dates, and reordering thresholds help ensure that you always have the right materials on hand without overstocking, which is particularly beneficial for hazardous materials with strict handling regulations.
Furthermore, integrating PlanetTogether with ERP systems facilitates material traceability, a crucial component of compliance in chemical manufacturing. With full traceability, you can quickly locate and recall any defective products, minimizing risks to both your facility and your customers.
Increased Operational Agility and Responsiveness
The chemical industry is highly dynamic, with frequent changes in customer demand, regulatory requirements, and raw material availability. As a result, operational agility is essential to maintain competitiveness. Integrating PlanetTogether with ERP systems such as Kinaxis enables your plant to be more responsive to these changes.
The combined power of PlanetTogether and your ERP gives you real-time visibility into every aspect of production, from order placement to final delivery. For instance, if a customer suddenly changes an order or a raw material becomes unavailable, the integrated system can quickly adjust production plans to accommodate the change, reducing downtime and keeping production on schedule.
With enhanced agility, you can respond to market changes faster and fulfill orders with greater accuracy. This responsiveness can improve customer satisfaction, which is especially valuable in an industry where quality and reliability are paramount.
Enhanced Quality Control and Compliance Management
Quality control and regulatory compliance are major concerns in chemical manufacturing. The integration of PlanetTogether with ERP systems like Aveva or Oracle provides a powerful solution for managing these critical aspects of your operation. By integrating quality control data directly into your production plans, you can catch potential issues early in the production process, reducing the likelihood of costly recalls or compliance violations.
This integration also enables automated compliance reporting. Instead of manually tracking and logging compliance-related data, you can rely on the integrated system to generate reports that meet regulatory requirements. This not only saves time but also ensures accuracy and consistency, reducing the risk of human error.
Additionally, real-time quality control data allows you to identify and address variations that could affect product quality. With PlanetTogether’s predictive capabilities, you can implement quality checks at optimal points in the production process, preventing defective products from reaching the market and safeguarding your facility’s reputation.
Optimized Resource Allocation and Maintenance Scheduling
In chemical manufacturing, effective resource allocation is essential to maintain productivity. Integrating PlanetTogether with ERP systems like SAP or Microsoft Dynamics allows for optimized resource allocation by providing real-time insights into equipment availability, workforce capacity, and material resources.
This integration enables you to assign resources more efficiently, ensuring that each production line operates at maximum capacity. It also helps you plan maintenance schedules in a way that minimizes disruption to production. For instance, if a machine requires routine maintenance, the system can automatically adjust the production schedule to avoid delays, allowing you to carry out maintenance during non-peak hours.
Additionally, predictive maintenance capabilities in PlanetTogether can help you identify potential equipment issues before they lead to breakdowns. By monitoring equipment performance in real-time, the system can predict when maintenance is needed and schedule it at the most convenient time, preventing costly downtime and extending the life of your equipment.
Data-Driven Insights for Continuous Improvement
One of the greatest advantages of integrating PlanetTogether with ERP systems is the ability to gather and analyze data from across your facility. With comprehensive insights into every aspect of your operation, you can identify areas for improvement and implement data-driven changes.
The analytics tools provided by this integration allow you to track key performance indicators (KPIs) such as production efficiency, equipment utilization, and defect rates. By continuously monitoring these KPIs, you can quickly spot trends and patterns, enabling proactive adjustments to optimize performance.
For example, if data shows that a particular process consistently experiences delays, you can investigate the root cause and make necessary changes. This continuous improvement approach can lead to significant efficiency gains, cost reductions, and productivity improvements over time.
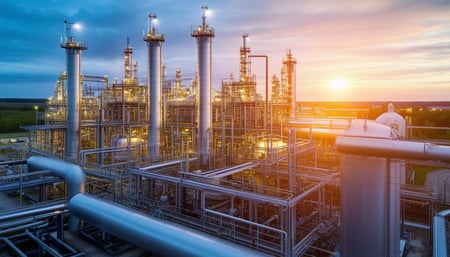
Achieving a Sustainable, Future-Ready Operation
Sustainability is becoming a top priority for chemical manufacturers, and integrated systems like PlanetTogether with SAP, Oracle, or Aveva can play a crucial role in achieving sustainable practices. By optimizing resource usage, reducing waste, and improving energy efficiency, you can minimize your facility’s environmental impact while also lowering costs.
For instance, by using real-time data to monitor energy consumption and material usage, you can identify opportunities to reduce waste and implement energy-efficient practices. This not only helps you meet regulatory requirements and customer expectations but also positions your facility as a leader in sustainable manufacturing.
In chemical manufacturing, the ability to coordinate every aspect of your operation is critical. Integrating PlanetTogether with ERP systems such as SAP, Oracle, Microsoft, Kinaxis, or Aveva provides a comprehensive solution for coordinating plant operations and meeting the demands of modern manufacturing.
With centralized data management, advanced scheduling, real-time inventory tracking, and predictive maintenance, you gain a powerful toolkit for improving efficiency, quality, and responsiveness. By leveraging data-driven insights, you can continuously improve operations and position your facility for long-term success.
Ultimately, the integration of PlanetTogether and ERP systems provides a competitive advantage, empowering you to keep pace with industry changes, exceed customer expectations, and lead your facility into a sustainable future.
Are you ready to take your manufacturing operations to the next level? Contact us today to learn more about how PlanetTogether can help you achieve your goals and drive success in your industry.