Continuous Flow Manufacturing Techniques
As a Production Planner, you're constantly seeking ways to optimize processes, minimize waste, and meet ever-changing consumer demands. One powerful strategy that can help achieve these goals is continuous flow manufacturing.
In this blog, we'll look into the principles of continuous flow manufacturing techniques and explore how integrating tools like PlanetTogether with ERP, SCM, and MES systems can enhance efficiency and streamline operations.
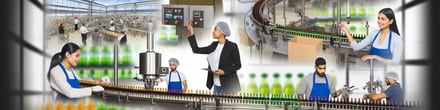
Continuous Flow Manufacturing
Continuous flow manufacturing is a lean production methodology focused on creating a smooth, uninterrupted flow of materials and processes throughout the production line. Unlike traditional batch manufacturing, where products move in discrete batches from one workstation to another, continuous flow manufacturing emphasizes a constant, steady flow of goods from raw materials to finished products.
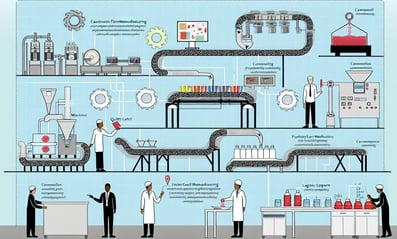
Key Principles of Continuous Flow Manufacturing
Just-In-Time (JIT) Production: JIT is a core principle of continuous flow manufacturing, aiming to produce goods only as needed, reducing excess inventory and minimizing storage costs.
Takt Time: Takt time refers to the rate at which products must be produced to meet customer demand. By aligning production with takt time, manufacturers can avoid overproduction and maintain a steady flow of goods.
Cellular Manufacturing: In continuous flow manufacturing, production is often organized into cells, with each cell dedicated to a specific task or process. This layout minimizes material handling and reduces lead times.
Pull System: A pull system, such as Kanban, is used to control the flow of materials through the production process. Workstations only produce goods when signaled by downstream demand, ensuring that resources are allocated efficiently.
Benefits of Continuous Flow Manufacturing
Reduced Lead Times: By eliminating batch processing and minimizing work in progress, continuous flow manufacturing can significantly reduce lead times, allowing for faster response to customer orders.
Lower Inventory Levels: JIT production and a pull-based system help keep inventory levels low, reducing carrying costs and freeing up capital for other investments.
Improved Quality: With a focus on standardized processes and continuous improvement, continuous flow manufacturing can lead to higher product quality and fewer defects.
Increased Flexibility: Continuous flow manufacturing allows for rapid changeovers and adjustments, making it easier to adapt to fluctuations in demand or product specifications.
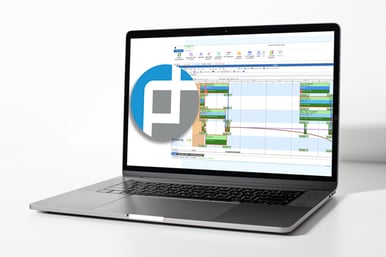
Integrating PlanetTogether with ERP, SCM, and MES Systems
While the principles of continuous flow manufacturing offer significant benefits, achieving optimal results requires effective coordination and synchronization of various production processes. This is where integration between advanced planning tools like PlanetTogether and ERP, SCM, and MES systems becomes invaluable.
PlanetTogether is a powerful production planning and scheduling software that allows manufacturers to optimize their production processes, balance capacity constraints, and minimize lead times. By integrating PlanetTogether with ERP systems such as SAP, Oracle, Microsoft Dynamics, or MES systems like Aveva, Kinaxis, or other industry-specific solutions, production planners can achieve seamless coordination between planning and execution phases.
Here's how integration between PlanetTogether and ERP, SCM, and MES systems enhances continuous flow manufacturing:
Real-Time Data Exchange: Integration allows for the seamless exchange of data between production planning software and other systems, ensuring that planners have access to up-to-date information on inventory levels, production schedules, and customer orders.
Improved Decision-Making: With accurate, real-time data at their fingertips, production planners can make informed decisions about production schedules, resource allocation, and inventory management, helping to optimize overall efficiency and minimize waste.
Enhanced Visibility and Traceability: Integration provides greater visibility into the entire production process, allowing planners to track materials, monitor progress, and identify bottlenecks or potential issues before they impact production.
Automated Workflows: By automating repetitive tasks and workflows, integration streamlines processes and reduces the risk of errors, allowing production planners to focus on higher-value activities such as strategic planning and optimization.
Scenario Planning and What-If Analysis: Integrated systems enable production planners to conduct scenario planning and what-if analysis, simulating different production scenarios and identifying the most efficient course of action to meet production goals while maximizing resource utilization.
Continuous flow manufacturing techniques offer a powerful framework for improving efficiency, reducing waste, and enhancing overall competitiveness in the food and beverage industry. By embracing principles such as JIT production, takt time, and pull systems, production planners can create a smoother, more streamlined production process that is better equipped to meet the demands of today's dynamic market.
Furthermore, by integrating advanced planning tools like PlanetTogether with ERP, SCM, and MES systems, companies can unlock even greater potential for optimization and efficiency. Through real-time data exchange, automated workflows, and enhanced visibility, integration empowers production planners to make informed decisions and drive continuous improvement across the entire production value chain.
Continuous flow manufacturing, coupled with strategic integration of planning and execution systems, holds the key to unlocking new levels of efficiency and competitiveness in the food and beverage manufacturing industry.
Are you ready to take your manufacturing operations to the next level? Contact us today to learn more about how PlanetTogether can help you achieve your goals and drive success in your industry.
LEAVE A COMMENT