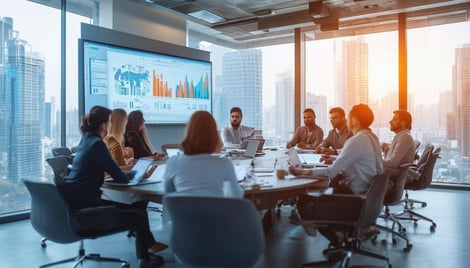
Collaborative Supply Chain Models
Supply chain management is more than a logistical exercise; it is a strategic differentiator. Traditional supply chain models often operate in silos, resulting in inefficiencies, delays, and misaligned objectives. However, the advent of collaborative supply chain models offers a transformative alternative, leveraging technology and cross-functional cooperation to drive efficiency, agility, and resilience.
For Supply Chain Managers, the integration of advanced planning systems like PlanetTogether with enterprise resource planning (ERP) tools such as SAP, Oracle, Microsoft, Kinaxis, or Aveva can revolutionize how supply chains are managed.
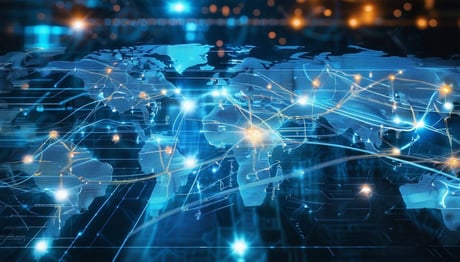
Understanding Collaborative Supply Chain Models
Collaborative supply chain models focus on creating partnerships among all stakeholders—suppliers, manufacturers, distributors, and customers—to achieve shared goals. Unlike traditional models, where each entity operates independently, collaboration ensures that every stakeholder aligns on objectives, shares data in real time, and works together to optimize performance.
Key benefits include:
Enhanced visibility: Stakeholders have access to real-time data across the supply chain.
Improved efficiency: Reduced redundancies and better resource utilization.
Greater resilience: Faster response to disruptions.
Increased profitability: Shared investments in innovation and cost-sharing initiatives.

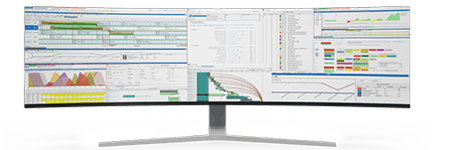
The Role of Technology in Collaboration
Technology serves as the backbone of collaborative supply chain models. Advanced tools and systems facilitate seamless communication, data sharing, and decision-making. In this context, integrating PlanetTogether’s advanced production planning and scheduling system with ERP platforms like SAP, Oracle, Microsoft, Kinaxis, or Aveva can unlock significant value.
Benefits of Integration:
Unified Data Streams: Integration ensures that all stakeholders work from a single source of truth, minimizing errors and improving coordination.
Real-Time Decision Making: PlanetTogether’s dynamic scheduling capabilities, when combined with real-time ERP data, enable agile responses to changing demand, supply disruptions, or production constraints.
Scenario Planning: With access to predictive analytics and what-if scenarios, managers can evaluate the impact of various decisions before implementation.
Enhanced Communication: Automated workflows and shared dashboards improve transparency and collaboration across departments and external partners.
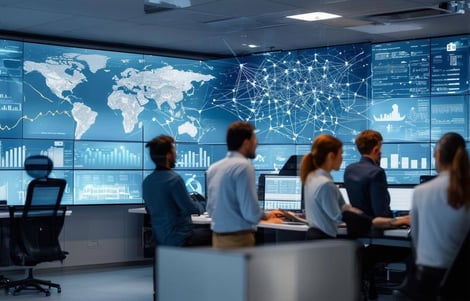
Implementing Collaborative Supply Chain Models
Align Objectives Across Stakeholders
The first step in implementing a collaborative supply chain model is ensuring that all stakeholders align on shared objectives. This alignment involves identifying key performance indicators (KPIs) that benefit all parties, such as on-time delivery rates, inventory turnover, and cost savings.
Leverage Technology for Integration
Choosing the right technology stack is critical. By integrating PlanetTogether with SAP, Oracle, Microsoft, Kinaxis, or Aveva, Supply Chain Managers can:
Create synchronized production plans.
Enhance inventory management through real-time visibility.
Ensure that production schedules align with supply chain constraints and opportunities.
For example, a manufacturer using SAP for ERP and PlanetTogether for production scheduling can ensure that procurement timelines match production needs, reducing excess inventory and stockouts.
Establish Real-Time Data Sharing
Real-time data sharing is the cornerstone of collaboration. By enabling data flow between PlanetTogether and ERP systems, organizations can:
Monitor production in real time.
Adjust schedules dynamically to meet demand fluctuations.
Collaborate more effectively with suppliers and distributors.
Foster a Collaborative Culture
Technology alone cannot ensure collaboration; a cultural shift is also necessary. Supply Chain Managers should encourage open communication, cross-functional teamwork, and a willingness to share information. Training programs and workshops can help align teams with collaborative practices.
Measure and Optimize
Continuous improvement is vital. Regularly evaluate the performance of the collaborative supply chain model against the established KPIs. Use analytics tools within PlanetTogether and ERP systems to identify areas for improvement, such as bottlenecks or inefficiencies.
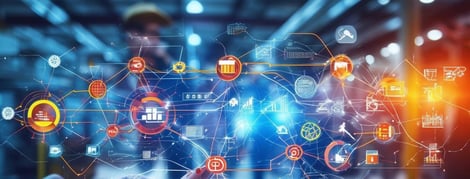
Overcoming Challenges in Collaborative Models
While collaborative supply chain models offer numerous benefits, they are not without challenges. Common obstacles include:
Resistance to Change: Employees and partners may resist new processes or technologies.
Solution: Invest in training and change management initiatives.
Data Security Concerns: Sharing data across organizations can pose security risks.
Solution: Use secure platforms and implement robust data governance policies.
Integration Complexity: Integrating PlanetTogether with ERP systems like SAP or Oracle can be complex.
Solution: Work with experienced implementation partners and ensure thorough testing before going live.
Collaborative supply chain models will become the norm rather than the exception. Emerging technologies such as artificial intelligence (AI), the Internet of Things (IoT), and blockchain will further enhance collaboration by enabling predictive analytics, smart contracts, and end-to-end traceability.
Collaborative supply chain models represent a paradigm shift for industrial manufacturing. By fostering alignment, leveraging technology, and embracing a culture of collaboration, organizations can achieve unparalleled efficiency, resilience, and profitability. Integrating PlanetTogether with SAP, Oracle, Microsoft, Kinaxis, or Aveva is a powerful step toward realizing these benefits. For Supply Chain Managers, the time to act is now—embrace collaboration and lead your organization into the future of manufacturing excellence.
Are you ready to take your manufacturing operations to the next level? Contact us today to learn more about how PlanetTogether can help you achieve your goals and drive success in your industry.
LEAVE A COMMENT