Collaborative Scheduling in Hybrid Environments
Manufacturers are constantly challenged with managing complex production schedules, maintaining optimal inventory levels, and ensuring seamless operation across all departments in the food and beverage manufacturing industry. To address these challenges, many are turning to advanced manufacturing IT solutions that facilitate collaborative scheduling in hybrid environments.
A prime example of such integration involves the combination of PlanetTogether's Advanced Planning and Scheduling (APS) software with leading Enterprise Resource Planning (ERP), Supply Chain Management (SCM), and Manufacturing Execution Systems (MES) such as SAP, Oracle, Microsoft, Kinaxis, and Aveva.
This blog aims to shed light on the strategic importance of collaborative scheduling in hybrid environments and how the right IT integrations can make a significant impact on manufacturing operations.
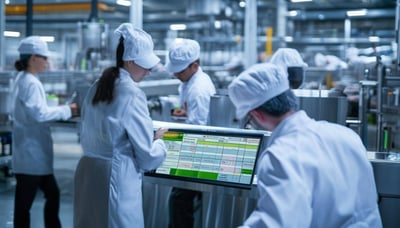
The Importance of Collaborative Scheduling
Collaborative scheduling is a strategic approach that enhances communication and cooperation across various departments and stakeholders within the manufacturing process. By implementing collaborative scheduling, food and beverage manufacturers can achieve:
Increased Transparency: All stakeholders have visibility into the scheduling process, which enhances communication and reduces conflicts.
Higher Flexibility: Adjustments to schedules can be made quickly in response to changes in demand, supply chain disruptions, or production issues.
Improved Efficiency: Optimized use of resources reduces downtime and minimizes waste.
Enhanced Responsiveness: Faster reaction times to market changes and customer demands.
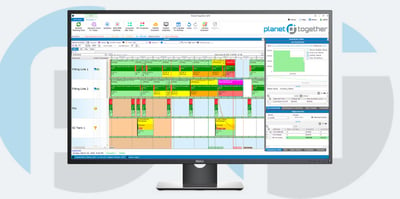
Integrating PlanetTogether with ERP, SCM, and MES Systems
PlanetTogether and SAP
SAP, being one of the leading ERP systems, is widely used in large-scale manufacturing facilities for its robust functionality that covers everything from procurement to production to sales. Integrating PlanetTogether’s APS with SAP enhances the ERP's capabilities by adding a layer of sophisticated scheduling and real-time decision support. The integration allows for:
- Real-Time Data Exchange: Scheduling decisions are based on real-time inventory levels, production capacity, and labor availability from SAP.
- Enhanced Resource Optimization: PlanetTogether's algorithms can optimize production schedules considering SAP’s data on material availability and delivery schedules.
- Scenario Planning: Users can create multiple "what-if" scenarios to understand the impact of different scheduling decisions, helping to foresee potential issues before they occur.
PlanetTogether and Oracle
Oracle ERP offers extensive functionalities for managing enterprise operations but can be complemented by PlanetTogether’s APS for more granular control over production scheduling. The synergy between Oracle and PlanetTogether allows manufacturing facilities to:
- Leverage Advanced Analytics: Oracle’s analytics combined with PlanetTogether’s scheduling tools enable deeper insights into production efficiency and resource utilization.
- Automate Scheduling Tasks: Reduce manual scheduling efforts, thereby freeing up resources for other critical activities.
- Improve Compliance and Reporting: Enhanced tracking and reporting features ensure that manufacturing processes comply with industry standards and regulations.
PlanetTogether and Microsoft Dynamics 365
Microsoft Dynamics 365 provides an adaptable ERP solution that integrates well with other Microsoft products and services. Integrating it with PlanetTogether allows facilities to leverage:
- Unified Operations: Seamless data flow between Dynamics 365 and PlanetTogether ensures that all stakeholders have access to up-to-date information.
- Enhanced User Experience: Users benefit from a familiar interface and integration with other Microsoft tools like Power BI for advanced reporting and analytics.
- Cloud-Based Flexibility: With both solutions offering cloud support, manufacturers can achieve greater scalability and accessibility.
Integration with Kinaxis and Aveva
Kinaxis and Aveva bring unique capabilities to the supply chain and operations management, which are greatly enhanced by integrating with PlanetTogether:
- Extended Supply Chain Visibility: Kinaxis users gain an advanced planning layer that enhances their ability to respond to supply chain disruptions.
- Operational Insight: Aveva’s focus on industrial operations gains an added layer of operational scheduling, making it easier to manage complex manufacturing processes.
Implementation Considerations
Implementing a collaborative scheduling system in a hybrid environment involves several critical steps:
Needs Assessment: Determine the specific needs and challenges of your facility.
System Selection: Choose the appropriate ERP, SCM, and MES systems that integrate well with PlanetTogether.
Data Integration: Ensure robust and secure integration that allows for real-time data exchange and system interoperability.
User Training: Equip your team with the necessary skills and knowledge to leverage the new systems effectively.
Continuous Improvement: Regularly review and optimize the scheduling system to adapt to new challenges and opportunities.
The integration of PlanetTogether with ERP, SCM and MES systems like SAP, Oracle, Microsoft Dynamics 365, Kinaxis, and Aveva transforms the landscape of manufacturing IT in the food and beverage industry. By facilitating collaborative scheduling, these integrations help manufacturers achieve unprecedented levels of efficiency, flexibility, and responsiveness.
Those who embrace these advanced IT solutions will find themselves well-equipped to meet the demands of the modern market and deliver value to their customers. Are you ready to take your manufacturing operations to the next level? Contact us today to learn more about how PlanetTogether can help you achieve your goals and drive success in your industry.
LEAVE A COMMENT