Cognitive Automation for Proactive Problem Resolution
Operations Directors are constantly on the lookout for ways to streamline processes, minimize downtime, and maximize productivity. Traditional methods of problem resolution often involve reactive approaches, where issues are addressed after they arise, leading to delays, disruptions, and increased costs.
However, in today's digital age, a new era of proactive problem resolution is emerging, thanks to the integration of cognitive automation technologies. These advanced systems leverage artificial intelligence (AI), machine learning (ML), and data analytics to predict and prevent potential issues before they occur, revolutionizing the way industrial manufacturing facilities operate.
In this blog, we'll explore the concept of cognitive automation and its role in driving proactive problem resolution within industrial manufacturing settings. Additionally, we'll look into the integration between PlanetTogether, a leading production planning and scheduling software, and prominent ERP, SCM, and MES systems like SAP, Oracle, Microsoft, Kinaxis, and Aveva, to showcase how these integrations further enhance operational efficiency.
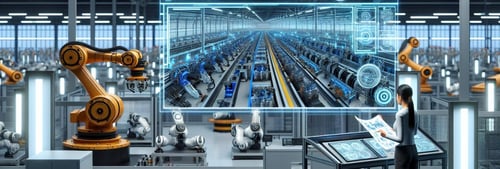
Understanding Cognitive Automation
Cognitive automation represents the next evolution in automation technologies. Unlike traditional automation systems that operate based on pre-defined rules and instructions, cognitive automation systems have the ability to learn, adapt, and make decisions autonomously.
At the core of cognitive automation are advanced algorithms that analyze vast amounts of data in real-time, identifying patterns, anomalies, and correlations that human operators may overlook. These systems continuously improve their performance through iterative learning, becoming increasingly adept at predicting and preempting potential issues.
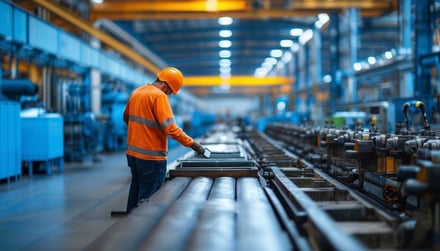
The Shift Towards Proactive Problem Resolution
In traditional manufacturing environments, problem resolution typically follows a reactive approach. When an issue arises, such as equipment failure, material shortages, or production bottlenecks, operators must respond swiftly to mitigate the impact on operations. However, this reactive mode of operation often leads to costly downtime, disruptions to production schedules, and inefficiencies in resource utilization.
Cognitive automation offers a paradigm shift by enabling proactive problem resolution. By analyzing historical data, monitoring real-time operational metrics, and employing predictive algorithms, these systems can anticipate potential issues before they manifest, allowing operators to take preventive measures to avoid disruptions and optimize performance.

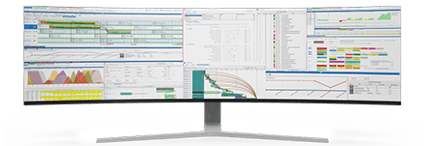
Integrating PlanetTogether with ERP, SCM, and MES Systems
Central to the success of cognitive automation in industrial manufacturing is the seamless integration of production planning and scheduling software like PlanetTogether with enterprise resource planning (ERP), supply chain management (SCM), and manufacturing execution systems (MES).
SAP Integration: By integrating PlanetTogether with SAP ERP, manufacturers gain end-to-end visibility into their operations, from order management to production planning. Real-time synchronization of data between the two systems enables intelligent decision-making based on up-to-date information, improving agility and responsiveness.
Oracle Integration: Oracle SCM integration with PlanetTogether enhances supply chain visibility and collaboration. Manufacturers can optimize production schedules based on real-time demand signals, inventory levels, and supplier capabilities, ensuring on-time delivery while minimizing inventory holding costs and stockouts.
Microsoft Integration: Integration between PlanetTogether and Microsoft Dynamics ERP streamlines production planning and execution processes. With seamless data exchange between the systems, manufacturers can achieve greater accuracy in demand forecasting, resource allocation, and scheduling, driving operational efficiency and customer satisfaction.
Kinaxis Integration: Kinaxis SCM integration with PlanetTogether enables agile and responsive supply chain operations. Manufacturers can leverage advanced analytics and scenario planning capabilities to proactively identify risks, simulate alternate production scenarios, and optimize resource utilization in dynamic environments.
Aveva Integration: Integration between PlanetTogether and Aveva MES enhances visibility and control over shop floor operations. Real-time data integration enables operators to monitor production performance, identify bottlenecks, and implement corrective actions in a timely manner, improving overall equipment effectiveness (OEE) and throughput.
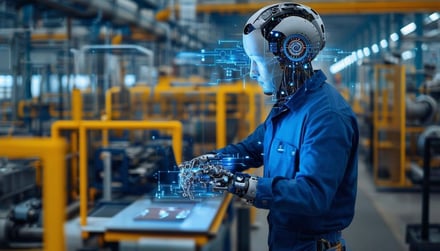
Benefits of Cognitive Automation in Industrial Manufacturing
The adoption of cognitive automation technologies in industrial manufacturing offers a multitude of benefits:
Predictive Maintenance: By analyzing equipment sensor data and historical maintenance records, cognitive automation systems can predict equipment failures before they occur, enabling proactive maintenance interventions to prevent downtime and extend asset lifespan.
Optimized Production Scheduling: Cognitive automation enables dynamic production scheduling based on real-time demand fluctuations, resource availability, and production constraints. This ensures optimal utilization of resources, minimizes lead times, and improves on-time delivery performance.
Inventory Optimization: Through advanced demand forecasting and inventory analytics, cognitive automation systems help manufacturers optimize inventory levels, reduce carrying costs, and prevent stockouts or excess inventory situations.
Enhanced Quality Control: By monitoring process variables and product quality metrics in real-time, cognitive automation systems can detect deviations from desired standards and trigger immediate corrective actions, minimizing defects and rework.
Improved Decision-Making: Cognitive automation empowers operators and decision-makers with actionable insights derived from data analysis, enabling informed decision-making and continuous process improvement.
Cognitive automation represents a transformative force in industrial manufacturing, enabling proactive problem resolution and driving operational excellence. By leveraging advanced AI, ML, and data analytics capabilities, manufacturers can anticipate and mitigate potential issues, optimize production processes, and stay ahead of the competition in today's dynamic business environment.
The integration between PlanetTogether and leading ERP, SCM, and MES systems further amplifies the benefits of cognitive automation, providing seamless data exchange, end-to-end visibility, and enhanced decision support capabilities.
As Operations Directors navigate the complexities of modern manufacturing, embracing cognitive automation is not just a competitive advantage but a strategic imperative for achieving sustainable growth, operational resilience, and customer satisfaction in the digital era.
Are you ready to take your manufacturing operations to the next level? Contact us today to learn more about how PlanetTogether can help you achieve your goals and drive success in your industry.