Cobots to the Production Floor
Production planners are constantly seeking innovative solutions to enhance efficiency, reduce downtime, and improve overall operational performance. The introduction of collaborative robots, or cobots, into production lines is emerging as a transformative strategy. Unlike traditional industrial robots, cobots are designed to work alongside human operators, fostering a harmonious interaction between man and machine. When coupled with advanced production planning and scheduling tools like PlanetTogether and integrated with systems such as SAP, Oracle, Microsoft, Kinaxis, or Aveva, the potential of cobots can be fully realized.
In this blog, we'll explore how the integration of cobots into production floors, alongside sophisticated planning tools, is reshaping the future of industrial manufacturing. We'll focus on the key benefits, the role of systems integration, and how production planners can navigate this new terrain to stay competitive and efficient.
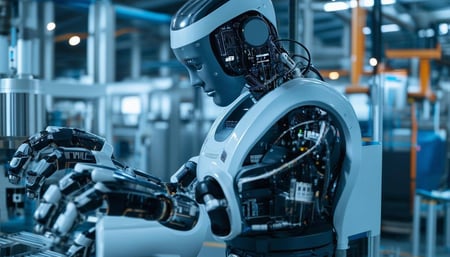
The Rise of Cobots: A Game-Changer in Manufacturing
Cobots have quickly gained traction in industrial settings due to their flexibility, ease of use, and ability to work safely alongside human workers without the need for extensive safety guarding. These robots are not only affordable compared to traditional robots, but they are also designed to assist in tasks that require precision, consistency, and repeatability, such as material handling, quality inspections, assembly, and packaging.
The growing demand for agility and adaptability in manufacturing processes is pushing cobots to the forefront. In sectors like automotive, electronics, food and beverage, and consumer goods, where product variation and customization are increasingly common, cobots offer a flexible and scalable solution. Production planners are now tasked with integrating these robots into production schedules in a way that optimizes workflow, reduces bottlenecks, and minimizes downtime.
Why Cobots?
From a production planning perspective, cobots offer several advantages that align with key manufacturing goals:
Increased Flexibility: Cobots can be easily reprogrammed to handle different tasks, making them ideal for facilities with varying product lines or frequent changeovers.
Improved Worker Safety and Productivity: Cobots can take over repetitive or dangerous tasks, allowing human workers to focus on more complex operations. This leads to fewer injuries and improved worker morale.
Scalability: Cobots can be easily deployed in both small and large facilities, providing scalability as production demands grow.
Cost Efficiency: With lower upfront costs and reduced maintenance compared to traditional robots, cobots provide a cost-effective solution for manufacturers looking to automate without extensive capital expenditure.
Enhanced Precision and Consistency: Cobots deliver a high level of precision, making them ideal for tasks that require consistent quality control. This reliability can significantly reduce waste and rework in production processes.

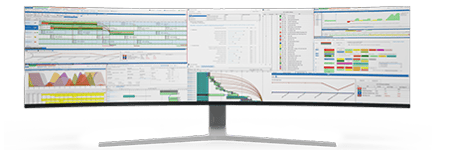
The Role of PlanetTogether and ERP Integration
For production planners, the integration of cobots into the production floor isn’t just about the physical deployment of these machines. It’s also about ensuring that these robots are part of a seamless, well-orchestrated production plan. This is where advanced planning and scheduling (APS) systems like PlanetTogether, integrated with leading enterprise resource planning (ERP) systems such as SAP, Oracle, Microsoft, Kinaxis, or Aveva, come into play.
PlanetTogether is a powerful tool that helps production planners optimize scheduling by providing real-time visibility into resource allocation, capacity planning, and material availability. When cobots are integrated into the production process, PlanetTogether can manage and optimize their workflows alongside human workers and other equipment, ensuring a balanced and efficient operation.
Key Benefits of Integration with ERP Systems
Real-Time Data Synchronization: Integration between PlanetTogether and ERP systems like SAP or Oracle allows for real-time data exchange. This ensures that cobot deployment is aligned with material availability, production schedules, and workforce planning, reducing the risk of delays or downtime.
Optimized Production Scheduling: Cobots require careful planning to ensure they are utilized effectively. With APS systems like PlanetTogether, production planners can create optimized schedules that account for both human workers and cobots, ensuring maximum efficiency and throughput.
Predictive Maintenance and Downtime Reduction: Integrating cobots with ERP systems enables predictive maintenance capabilities. This means that planners can monitor the health of cobots and schedule maintenance before a breakdown occurs, reducing unexpected downtime.
Improved Resource Allocation: Through integration with ERP systems, production planners can better allocate cobots to specific tasks based on real-time demand, labor availability, and material constraints.
Seamless Communication and Coordination: With cobots integrated into a digital workflow through systems like PlanetTogether and SAP or Microsoft, production planners can communicate changes in production schedules, materials availability, or machine downtimes in real time, enabling rapid adjustments and minimizing disruptions.
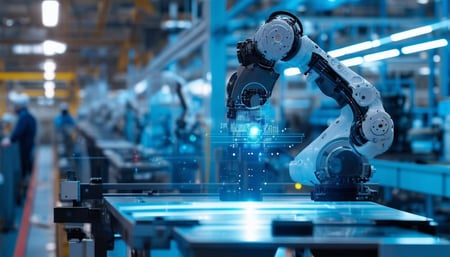
Cobots and Advanced Scheduling: The New Workflow
To maximize the benefits of cobots on the production floor, a collaborative approach between machines, people, and planning systems is essential. Here’s how production planners can optimize their workflows:
Assess Tasks for Automation: Not all tasks are suitable for cobots. Production planners must assess which processes can benefit most from automation, such as repetitive, precision-driven tasks. Cobots should complement human workers, taking on tasks that enhance efficiency while leaving complex decision-making to humans.
Develop a Collaborative Production Schedule: A collaborative production schedule considers both human workers and cobots. Using tools like PlanetTogether, planners can create schedules that optimize the balance between human and machine efforts. For instance, cobots may be programmed to handle assembly tasks during peak demand periods, while humans focus on quality control and decision-making.
Leverage Real-Time Analytics: Integration between PlanetTogether and ERP systems allows production planners to access real-time data on cobot performance, material availability, and production status. This information enables planners to make informed decisions about workflow adjustments, bottlenecks, and task allocation.
Monitor Performance and Adjust: Once cobots are deployed, it’s critical to monitor their performance and make adjustments as needed. Continuous improvement processes, facilitated by real-time data from integrated systems like SAP or Oracle, allow for tweaking of production schedules, task assignments, and resource allocation to ensure optimal performance.
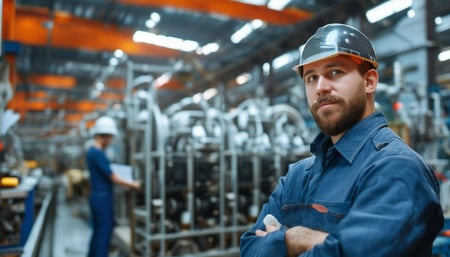
Overcoming Challenges: What Production Planners Need to Consider
While cobots offer tremendous potential, there are challenges that production planners need to consider when integrating them into the production floor:
Worker Training: Human workers need to be trained to work alongside cobots. This includes safety protocols, programming, and basic troubleshooting skills. Planners must allocate time and resources for this training.
Customization and Flexibility: Cobots need to be programmed for specific tasks, which can vary from facility to facility. Production planners must ensure that cobots are flexible enough to handle different product lines or shifts in production demand.
Data Management: Integrating cobots with ERP and APS systems requires effective data management. Planners must ensure that data from cobots is collected, analyzed, and utilized to optimize production schedules and maintenance needs.
The integration of cobots into the production floor represents a significant shift in how industrial manufacturers approach automation. For production planners, the ability to manage both human and machine resources through advanced scheduling tools like PlanetTogether, integrated with ERP systems such as SAP, Oracle, or Microsoft, opens up new possibilities for efficiency, scalability, and cost savings.
As cobots become more widespread in industrial settings, production planners will play a crucial role in ensuring their successful deployment. By leveraging the power of real-time data, predictive maintenance, and optimized scheduling, planners can maximize the benefits of cobots, driving their facilities towards a future of smart, efficient, and collaborative manufacturing.
Are you ready to take your manufacturing operations to the next level? Contact us today to learn more about how PlanetTogether can help you achieve your goals and drive success in your industry.