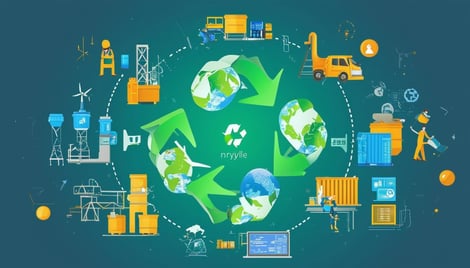
Circular Manufacturing Scheduling: A Roadmap for Production Planners in Chemical Manufacturing
Chemical manufacturing faces growing pressure to adopt sustainable practices. The traditional linear production model—which follows a "take, make, dispose" approach—is no longer sufficient to meet environmental, regulatory, and economic demands. Instead, the shift toward circular manufacturing is gaining momentum, emphasizing resource efficiency, waste reduction, and closed-loop systems.
For Production Planners in chemical manufacturing, the adoption of circular principles introduces a new layer of complexity and opportunity. Effective scheduling becomes pivotal in balancing sustainability goals with production efficiency. Tools like PlanetTogether, when integrated with enterprise systems like SAP, Oracle, Microsoft, Kinaxis, or Aveva, can play a transformative role in this transition.
This blog explores the concept of circular manufacturing scheduling, its significance for chemical production, and how integrating advanced planning systems can drive meaningful outcomes.
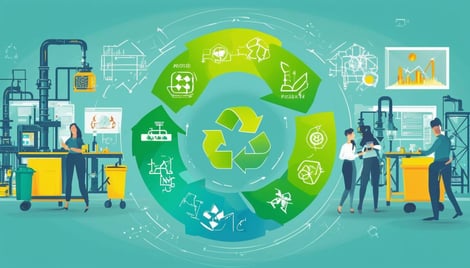
What is Circular Manufacturing Scheduling?
Circular manufacturing scheduling aligns production planning with the principles of the circular economy. This approach focuses on:
Resource Optimization: Prioritizing the use of recycled or renewable inputs.
Waste Minimization: Scheduling processes to maximize yield and reduce by-products.
Material Recovery: Coordinating the reintegration of waste streams into production.
Sustainability Metrics: Incorporating environmental factors, such as carbon footprint and energy efficiency, into planning decisions.
In chemical manufacturing, where processes are often resource-intensive and generate significant waste, adopting a circular scheduling model can reduce costs, enhance regulatory compliance, and support corporate sustainability goals.
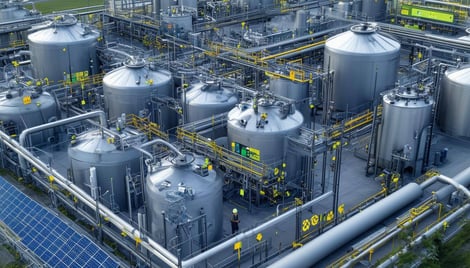
The Challenges for Production Planners
Transitioning to circular manufacturing presents unique challenges for Production Planners:
Complex Material Flows: Managing the interplay between raw materials, recycled inputs, and by-products.
Dynamic Supply Chains: Coordinating suppliers, recycling facilities, and logistics to ensure a steady flow of inputs.
Regulatory Compliance: Navigating stringent environmental regulations and reporting requirements.
Unpredictable Demand: Adjusting schedules to account for fluctuations in product demand and availability of recycled materials.
Technology Integration: Leveraging advanced tools to analyze and optimize schedules in real-time.
Addressing these challenges requires a robust planning and scheduling framework supported by cutting-edge technology.

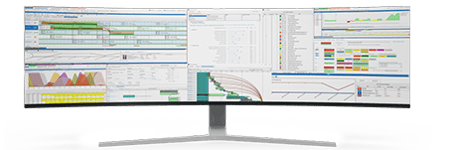
Role of PlanetTogether in Circular Scheduling
PlanetTogether’s advanced planning and scheduling (APS) platform is uniquely suited to enable circular manufacturing scheduling. Its capabilities include:
Real-Time Visibility: Provides a comprehensive view of production activities, material flows, and inventory levels.
Scenario Planning: Enables planners to simulate different scheduling scenarios and evaluate their impact on sustainability and efficiency.
Integration with ERP Systems: Seamlessly connects with enterprise platforms like SAP, Oracle, Microsoft Dynamics, Kinaxis, or Aveva to unify data and processes.
Constraint Management: Accounts for production constraints such as material availability, machine capacity, and energy consumption.
Sustainability Analytics: Tracks key performance indicators (KPIs) related to waste reduction, energy efficiency, and carbon emissions.
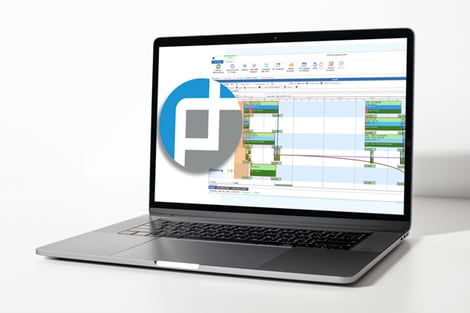
Integration with Enterprise Systems: Unlocking Synergies
Integrating PlanetTogether with systems like SAP, Oracle, Microsoft, Kinaxis, or Aveva amplifies its impact, creating a cohesive ecosystem for circular scheduling. Here’s how these integrations can drive value:
Data Synchronization
Real-time data exchange between PlanetTogether and ERP systems ensures that planners have access to accurate information on inventory, orders, and production.
Example: Integration with SAP’s Material Management (MM) module can provide insights into the availability of recycled materials and procurement schedules.
Enhanced Collaboration
Cross-functional collaboration becomes seamless, allowing teams across procurement, production, and logistics to align on sustainability goals.
Example: Microsoft Dynamics’ collaborative tools can facilitate communication and data sharing within teams.
Advanced Analytics
Combined analytics capabilities provide actionable insights, helping planners optimize schedules for cost, efficiency, and sustainability.
Example: Kinaxis’ supply chain planning tools, integrated with PlanetTogether, can predict the impact of material recovery strategies on overall production.
Compliance Reporting
Automated reporting tools ensure compliance with environmental regulations and corporate sustainability standards.
Example: Aveva’s process management capabilities can track emissions and waste metrics for reporting purposes.
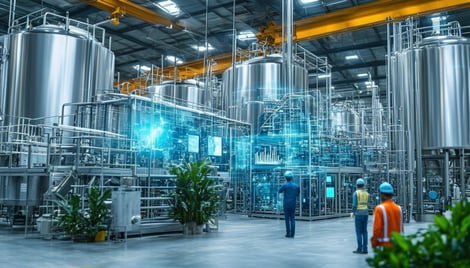
Practical Strategies for Circular Scheduling
To effectively implement circular scheduling in chemical manufacturing, Production Planners can adopt the following strategies:
Prioritize High-Impact Areas
Identify processes with the highest potential for resource recovery and waste reduction.
Example: Focus on recycling solvents or repurposing by-products in production.
Leverage Predictive Analytics
Use advanced analytics to forecast demand, predict material availability, and optimize schedules.
Example: Predictive maintenance data can help schedule machine downtime, minimizing disruption and energy use.
Implement Closed-Loop Systems
Design schedules that facilitate the reintegration of waste streams into production.
Example: Coordinate with suppliers to return packaging materials for reuse.
Monitor Sustainability Metrics
Incorporate KPIs such as energy consumption, waste generation, and carbon emissions into scheduling decisions.
Example: Use PlanetTogether’s sustainability analytics to identify opportunities for improvement.
Engage Stakeholders
Collaborate with suppliers, customers, and internal teams to create a shared vision for circular manufacturing.
Example: Partner with recycling facilities to ensure a steady supply of recovered materials.
Benefits of Circular Scheduling
Adopting circular manufacturing scheduling offers significant benefits for chemical manufacturers:
Cost Savings
Reduced material and waste disposal costs through resource recovery and optimization.
Enhanced Efficiency
Streamlined processes and improved utilization of resources and assets.
Regulatory Compliance
Simplified compliance with environmental standards and reporting requirements.
Sustainability Leadership
Strengthened brand reputation and alignment with global sustainability initiatives.
Resilience
Increased flexibility and adaptability in the face of supply chain disruptions and market shifts.
Circular manufacturing scheduling is more than a trend—it’s a requirement for the future of chemical manufacturing. By integrating PlanetTogether with enterprise systems, Production Planners can navigate the complexities of this transition and unlock new opportunities for efficiency, sustainability, and growth.
The time to act is now. Equip your team with the tools and strategies needed to embrace circular scheduling and shape a sustainable future for your organization.
Are you ready to take your manufacturing operations to the next level? Contact us today to learn more about how PlanetTogether can help you achieve your goals and drive success in your industry.