If you feel as if your production facility is failing to meet production schedules and you are experiencing overstock or high costs, then you may be considering investing in an enterprise resource planning (ERP) system to alleviate these issues. Enterprise resource planning (ERP) has become a necessity among manufacturing facilities that are seeking to maintain their competitive edge against other production facilities.
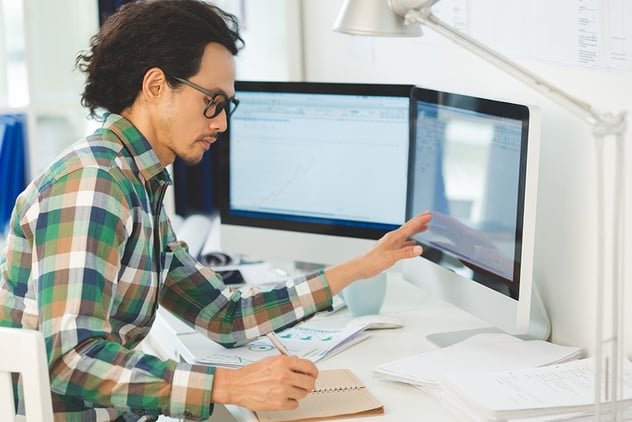
An enterprise resource planning (ERP) system manages all the information about a company’s products, customers, suppliers, and employees. These computerized systems are designed to support and integrate the organizational processes across functional boundaries within the business, as well as calibrate and control all of the resources within a manufacturing facility.
There are three main reasons why companies choose to implement an ERP system into their organization:
- To integrate financial data - An ERP system creates a single version of the truth to align everyone in the company in terms of costs and revenues.
- To standardize manufacturing processes - An ERP system ensures that different units are using the same business processes to save time and increase productivity.
- To standardize HR information - An ERP system can help large companies have a standard way of tracking employee time and share benefits and services offered.
Utilizing an enterprise resource planning (ERP) system can aid your production facility immensely but it is important to understand its basic characteristics before implementing this type of software.
Four Characteristics of Enterprise Resource Planning (ERP)
The four characters of an enterprise resource planning (ERP) system includes the following:
- Modular Design - The modular design of an ERP system incorporates distinct business modules such as manufacturing, financial, accounting, and distribution. Each module takes care of various functions of a particular section or department within your organization. While these modules can operate separately, they are integrated inside the ERP system to provide a seamless flow of data and information between all modules. This ultimately will enlarge the operational transparency provided for by the standard interface. These separate modules work in real-time with online and batch-processing capabilities.
- Central Common Database - Implementing a common centralized database management system, which is also called a DBMS, is an important characteristic of an advantageous ERP system. All data is entered and stored only once and then utilized by all departments simultaneously which helps eliminate data-entry errors and other flaws associated with using a distributed database.
- Flexible and Open Database - Organizations are almost always dynamic in nature, which is where ERP systems offer flexibility to respond to the changing needs of the enterprise. These systems have an open system architecture, allowing them to attach or detach any module as and when required without affecting the other modules. An advantageous ERP system should support connectivity to other business entities within the organization and shouldn’t be confined within the boundaries of a manufacturing facility.
- Automatic Generation of Information - An ERP system provides business intelligence tools such as executive information systems, decision support systems, easy warning systems, and more. These tools help manufacturing operations to make data-based decisions that pertain to their overall production process. All financial and business information will be automatically generated from the data that is found in the centralized database of the ERP system.
While an ERP system can offer great benefits for manufacturers, any facility looking to improve its operation’s efficiency and output should consider combining the benefits of an Advanced Planning and Scheduling (APS) system with their ERP.
An Advanced Planning and Scheduling (APS) software is a production planning software that allows manufacturers to have a visual representation of their overall production process and fills in the gaps where an ERP system may lack.
The whole company over here genuinely loves the capabilities, the connection to Goldratt in our planning, and the entire experience. PlanetTogether has improved our Production Meetings, the way we run Overtime Planning, backward scheduling, long-running programs, materials planning, and on and on…
CHUCK DIPIETRO, DIRECTOR OF PROCUREMENT & PLANNING, BEMA INCORPORATED
The main problem with ERP software is that, despite its multitude of functions, it lacks the strategic decision-making functions that an Advanced Planning and Scheduling system has.
Though an ERP and an APS system can be used independently, they work best when combined together. Without an ERP system, an APS application cannot perform rapid decision-making functions when changes are made in supply, demand, and manufacturing processes. For companies specializing in manufacturing, logistics, and distribution, a real-time analysis and simulation function offered by an APS system is necessary to keep costs low and efficiency high.
Advanced Planning and Scheduling (APS) Software
Advanced Planning and Scheduling Softwares have become a must for modern-day manufacturing operations as customer demand for increased product assortment, fast delivery, and downward cost pressures become prevalent. These systems help planners save time while providing greater agility in updating ever-changing priorities, production schedules, and inventory plans. APS Systems can be quickly integrated with an ERP/MRP software to fill the gaps where these systems lack planning and scheduling flexibility, accuracy, and efficiency.
With PlanetTogether APS you can:
- Create optimized schedules that balance production efficiency and delivery performance
- Maximize throughput on bottleneck resources to increase revenue
- Synchronize supply with demand to reduce inventories
- Provide company-wide visibility to resource capacity
- Enable scenario data-driven decision making
The implementation of an Advanced Planning and Scheduling (APS) Software will take your manufacturing operations to the next level of production efficiency by taking advantage of the operational data you already possess in your ERP system. APS is a step in the right direction of efficiency and lean manufacturing production enhancement. Try out a free trial or demo!
Related Capacity Video
APS Resources