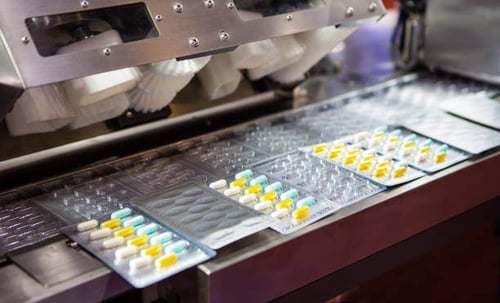
Category Management in Pharmaceutical Manufacturing: A Strategic Approach for Production Schedulers
In pharmaceutical manufacturing, where precision, efficiency, and regulatory compliance are essential, production schedulers play a critical role in ensuring seamless operations. One strategic approach that can significantly enhance scheduling efficiency is Category Management—a methodology that segments procurement and production planning into distinct categories to drive better decision-making, cost optimization, and resource allocation.
When coupled with advanced Advanced Planning and Scheduling (APS) systems like PlanetTogether, and seamlessly integrated with SAP, Oracle, Microsoft, Kinaxis, or Aveva, category management becomes a powerful tool for optimizing supply chain operations in pharmaceutical production.
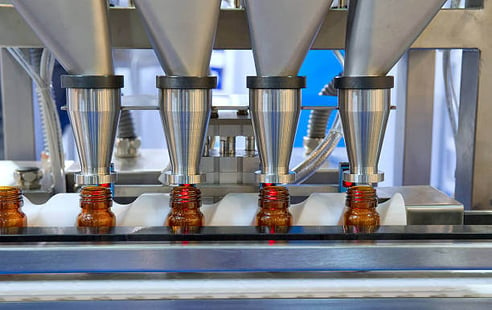
Understanding Category Management in Pharmaceutical Manufacturing
Category management involves organizing materials, suppliers, and production schedules into manageable categories based on their attributes, criticality, and usage. The core objective is to standardize procurement, reduce risks, and improve production flow, all while ensuring compliance with regulatory bodies like the FDA, EMA, or WHO.
For a production scheduler, category management impacts multiple facets of daily operations:
Raw Material Planning: Categorizing raw materials by potency, stability, supplier reliability, and lead times.
Batch Scheduling: Grouping production runs based on drug classification, common excipients, or sterilization requirements.
Supply Chain Coordination: Aligning procurement, storage, and production schedules based on category-specific demands.
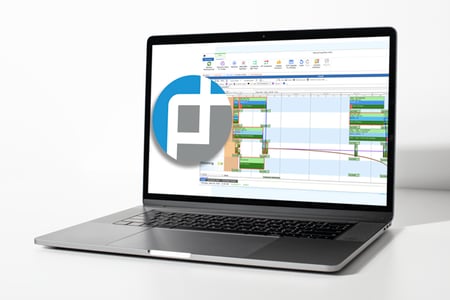
The Role of APS in Category Management
An Advanced Planning and Scheduling (APS) system like PlanetTogether takes category management to the next level by automating scheduling decisions, optimizing resource allocation, and providing real-time visibility into the production process.
Some key benefits of APS in category management include:
Automated Scheduling: APS assigns production tasks based on predefined categories, minimizing conflicts and reducing idle time.
Capacity Optimization: By understanding category-specific constraints, the system optimally distributes workloads across available resources.
Regulatory Compliance: Helps ensure category-specific compliance measures are met (e.g., preventing cross-contamination, maintaining required environmental conditions).
Real-time Adjustments: Any supply chain disruptions can be mitigated by rescheduling within category constraints without impacting production flow.
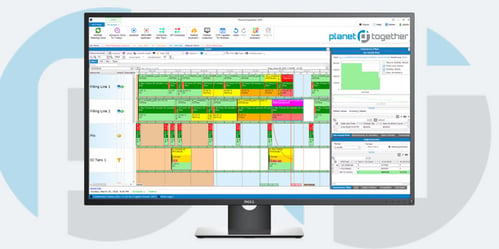
Integrating PlanetTogether with ERP Systems: A Game Changer
The effectiveness of category management in production scheduling is further amplified when PlanetTogether APS is integrated with major ERP systems like SAP, Oracle, Microsoft, Kinaxis, or Aveva. This integration enables seamless data exchange between procurement, inventory management, and scheduling systems.
How ERP-APS Integration Enhances Category Management
Real-time Inventory Tracking
ERP systems manage inventory levels, while PlanetTogether ensures raw material consumption aligns with category-based production needs.
Prevents material shortages and excess stock buildup.
Automated Demand Forecasting
ERP’s historical data and demand trends feed into APS, ensuring category-based scheduling reflects real-time market demands.
Regulatory Documentation and Compliance
Integrated systems ensure that category-specific compliance documentation is linked to production schedules, reducing audit risks.
Supplier Collaboration
Category-based procurement strategies can be aligned with supplier capabilities, lead times, and quality metrics.
Real-time visibility into supplier reliability through ERP-APS integration ensures scheduling decisions are data-driven.
Implementing Category Management in Your Facility
To successfully implement category management in pharmaceutical scheduling, consider the following steps:
Analyze Current Scheduling Practices
Identify inefficiencies in current workflows and categorize raw materials and production processes.
Integrate APS with ERP
Ensure seamless data synchronization between systems for real-time decision-making.
Develop Category-Specific Policies
Define criteria for each category, including sourcing, production scheduling, and compliance measures.
Utilize Advanced Analytics
Leverage APS reporting tools to monitor key performance indicators (KPIs) for each category.
Train Your Team
Ensure production schedulers, procurement teams, and quality assurance personnel understand the principles of category management.
For production schedulers in pharmaceutical manufacturing, category management offers a structured approach to improving efficiency, reducing waste, and ensuring compliance. When integrated with PlanetTogether APS and ERP systems like SAP, Oracle, Microsoft, Kinaxis, or Aveva, the benefits are amplified, creating a synchronized, optimized, and compliant production environment.
By adopting category-based scheduling, pharmaceutical companies can achieve greater agility, improved resource utilization, and enhanced regulatory adherence—paving the way for a more resilient and competitive manufacturing operation.
Are you ready to take your manufacturing operations to the next level? Contact us today to learn more about how PlanetTogether can help you achieve your goals and drive success in your industry.
LEAVE A COMMENT