Capacity Planning for Rapid Changes in Demand
In the industrial manufacturing environment, demand volatility is becoming the norm rather than the exception. Production planners are facing pressures to manage sudden shifts, optimize capacity, and balance resources without sacrificing quality or timelines. Capacity planning is the cornerstone for achieving this flexibility, enabling planners to quickly respond to unexpected demand while maximizing efficiency.
The integration of advanced capacity planning tools like PlanetTogether with ERP and planning systems, such as SAP, Oracle, Microsoft, Kinaxis, and Aveva, can significantly enhance your ability to make fast, data-driven decisions in the face of demand fluctuations.
In this blog, we’ll explore strategies to optimize capacity planning for rapid changes in demand and dive into how PlanetTogether’s integrations with popular ERP systems can streamline these processes.
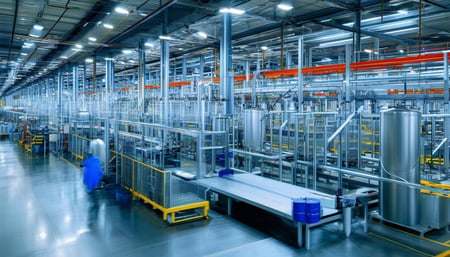
Capacity Planning in the Face of Demand Surges
Capacity planning is the process of determining the production volume a facility can handle to meet demand while keeping resources in balance. In a steady environment, capacity planning may involve straightforward adjustments. However, when demand surges unexpectedly, industrial manufacturers often face challenges such as resource shortages, machine downtimes, and extended lead times. With the help of integrated planning solutions, these challenges can be mitigated, making it possible to not only forecast needs but respond to them in real-time.
Let’s break down some primary elements in capacity planning to respond effectively to sudden demand shifts:
Forecasting: Demand forecasting helps you understand potential surges. PlanetTogether’s demand forecasting capabilities can be enhanced with historical and real-time data integration from SAP or Oracle, allowing you to plan based on reliable insights.
Resource Utilization: Effective capacity planning involves balancing workloads to prevent bottlenecks and underutilization. Integrated systems allow you to track the capacity of each machine, production line, or resource in real time.
Production Scheduling: Scheduling is essential for meeting demand shifts without causing production delays. PlanetTogether’s advanced scheduling can dynamically update and adjust based on incoming data from ERP systems, allowing you to manage sudden demand spikes.

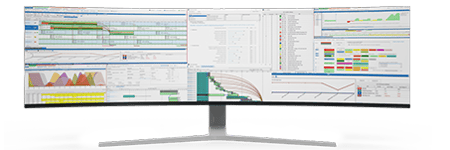
Key Benefits of Integrating PlanetTogether with Leading ERP Systems
PlanetTogether’s integration with systems like SAP, Oracle, Microsoft, Kinaxis, and Aveva brings essential data sources together into one cohesive view. This connection empowers production planners with robust, real-time insights to plan capacity more effectively. Here’s a breakdown of the benefits:
Enhanced Data Visibility
Integrating PlanetTogether with your ERP systems allows you to consolidate data across production, inventory, and supply chain processes. For example, real-time inventory levels from SAP combined with machine availability data in PlanetTogether give you a complete picture of available capacity.
Improved Demand Forecasting and Real-Time Adjustments
By pulling historical and current demand data from ERP systems like Oracle and Kinaxis, PlanetTogether helps you adapt to demand changes with predictive accuracy. With synchronized data, the system can forecast based on seasonal trends, economic factors, or external events, enabling you to prepare for fluctuating demand.
Efficient Resource Allocation and Capacity Management
Real-time resource allocation capabilities allow PlanetTogether to automatically schedule resources by balancing workloads, reallocating machines, and deploying workers where they’re most needed. This seamless integration minimizes bottlenecks and underutilized resources, ensuring that production lines remain operational during demand surges.
Agility and Responsiveness through Collaborative Planning
Integration between PlanetTogether and Aveva, for example, allows for collaborative, multi-department planning. Production planners, along with operations and supply chain teams, can access and modify plans based on shared data, supporting quick adjustments when demand surges occur.
Reduced Lead Times and Operational Costs
By automating and optimizing capacity planning, you can reduce lead times and lower operational costs. For instance, SAP and Microsoft integrations provide access to supplier data and delivery schedules, allowing PlanetTogether to help you reconfigure production schedules and maintain optimal inventory levels without unnecessary holding costs.
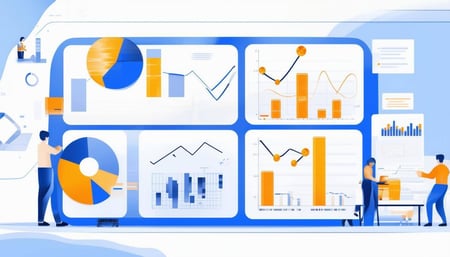
Capacity Planning Strategies for Rapid Demand Changes
With the integration between PlanetTogether and your ERP systems, you can adopt advanced strategies to improve capacity planning and manage sudden demand shifts. Here are some practical steps to guide your approach:
1. Implement Dynamic Forecasting
By integrating data from systems like Oracle or Kinaxis, you can set up dynamic forecasting models in PlanetTogether that automatically adjust to market trends, customer orders, or seasonal variations. This dynamic approach allows you to capture demand surges early, preparing your facility to handle increased production with minimal lead time.
2. Adopt Flexible Scheduling Practices
Use PlanetTogether’s real-time scheduling capabilities, enhanced by data from SAP or Aveva, to quickly adjust production lines and reallocate resources when demand spikes. Flexible scheduling allows you to add or remove shifts, manage overtime, or redistribute workers across different production areas.
3. Balance Resource Utilization
Capacity planning relies on optimal resource utilization. Integration with systems like Microsoft allows you to gather comprehensive data on machine health, maintenance schedules, and labor availability. This visibility enables you to distribute workloads evenly across machines and production lines, reducing the risk of bottlenecks.
4. Develop Contingency Plans
With real-time data integration, you can set up contingency plans to pre-emptively manage high-demand scenarios. For example, integration with Aveva may offer predictive insights on production slowdowns or equipment needs, giving you enough time to make the necessary adjustments.
5. Leverage AI and Machine Learning for Predictive Insights
PlanetTogether, integrated with ERP systems like SAP and Oracle, can support machine learning algorithms that analyze production patterns and suggest optimal capacity adjustments. AI-driven insights make it possible to predict when a demand surge is likely and how best to prepare for it, keeping operations lean and effective.
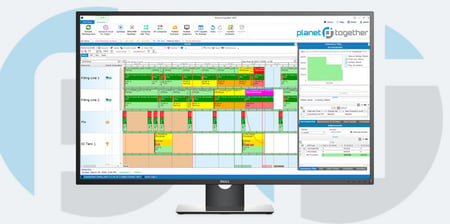
Maximizing the Potential of ERP Integration with PlanetTogether
Achieving efficient capacity planning requires leveraging the full potential of PlanetTogether’s integration with ERP systems. Here are some best practices:
Continuous Training and Process Improvement: Familiarize your team with the functionality offered by PlanetTogether and your ERP integrations. Regular training sessions ensure that planners, operators, and managers understand how to use the data for strategic planning.
Monitor KPIs for Continuous Improvement: Use key performance indicators (KPIs) such as machine utilization rates, inventory levels, and lead times to assess capacity planning effectiveness. The integrated platform can provide real-time KPIs, giving you insights into operational improvements.
Refine Data Quality and Accuracy: Ensure that data flowing from ERP systems like Oracle or SAP into PlanetTogether is accurate and up-to-date. Data quality is essential for predictive modeling, AI applications, and effective decision-making.
Managing sudden changes in demand in industrial manufacturing is a complex task that requires agility, precision, and real-time data. By integrating PlanetTogether with powerful ERP systems like SAP, Oracle, Microsoft, Kinaxis, or Aveva, production planners can take a proactive, data-driven approach to capacity planning. This integration empowers planners with tools to forecast demand, adjust schedules, optimize resources, and respond to rapid shifts effectively.
As demand volatility continues to shape the manufacturing landscape, advanced capacity planning will be a critical asset for maintaining competitive advantage. Leveraging the full power of integrated systems, production planners can confidently navigate sudden demand changes, keeping production lines efficient and customers satisfied.
Are you ready to take your manufacturing operations to the next level? Contact us today to learn more about how PlanetTogether can help you achieve your goals and drive success in your industry.