Capacity Planning Best Practices
For Plant Managers in the packaging manufacturing industry, capacity planning is the cornerstone of achieving operational excellence. In today's fast-paced market environment, the ability to efficiently manage production capacity directly influences the competitive edge and profitability of a manufacturing facility.
This blog looks into best practices for capacity planning, with a special focus on integrating advanced planning and scheduling (APS) solutions like PlanetTogether with major ERP (Enterprise Resource Planning), SCM (Supply Chain Management), and MES (Manufacturing Execution Systems) platforms such as SAP, Oracle, Microsoft, Kinaxis, and Aveva.
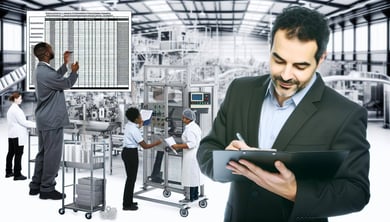
Understanding Capacity Planning in Packaging Manufacturing
Capacity planning in a packaging manufacturing facility involves forecasting production needs and adjusting resources to meet these demands without overshooting costs. It's a delicate balance between maximizing the use of available resources and meeting production targets within the set timelines.
Key Challenges in Capacity Planning
Demand Volatility: Packaging needs can fluctuate drastically due to consumer trends, seasonal demands, and other market dynamics.
Resource Constraints: Limited availability of machinery, labor, and materials can hinder the ability to ramp up production as needed.
Technological Integration: Seamlessly integrating new technologies with existing systems without disrupting the production flow.

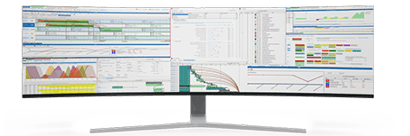
Integrating PlanetTogether: Leveraging Technology for Enhanced Visibility and Control
Integrating an APS like PlanetTogether with your existing ERP, SCM, or MES systems is crucial. This integration allows for a seamless flow of information across all platforms, enhancing visibility into every aspect of the manufacturing process.
Integrating with SAP
SAP, being one of the leading ERP systems, offers robust capabilities for managing complex manufacturing processes. Integrating PlanetTogether with SAP can help synchronize production planning and inventory management, leading to optimized machine scheduling and reduced downtime.
Oracle Integration
Oracle’s ERP solutions provide extensive SCM and manufacturing functionalities. When integrated with PlanetTogether, plant managers can leverage real-time data analytics to make informed decisions about production scheduling, labor allocation, and materials management.
Microsoft Dynamics 365
For users of Microsoft Dynamics 365, integrating with PlanetTogether means enhancing the flexibility of manufacturing operations with advanced data insights and predictive analytics capabilities. This integration helps in adjusting production schedules quickly in response to changing market demands.
Kinaxis Integration
Kinaxis offers specialized solutions for supply chain management that focus on rapid response and scenario analysis. Combining this with the scheduling capabilities of PlanetTogether allows for dynamic adjustment of production plans to align with supply chain changes.
Aveva Connectivity
Aveva’s focus on industrial software gets a boost when integrated with an APS like PlanetTogether. This combination enhances digital transformation efforts in packaging manufacturing by providing deeper insights into equipment efficiency and maintenance schedules.
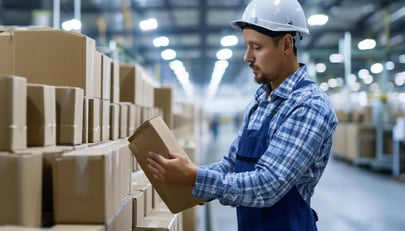
Best Practices in Capacity Planning
Adopt a Demand-Driven Planning Approach
Utilize advanced forecasting tools to understand market trends and customer preferences. This approach allows for adjusting production capacity in advance, preventing both overproduction and stockouts.
Focus on Continuous Improvement
Implement lean manufacturing principles to identify and eliminate waste in the production process. Continuous monitoring and analysis of production data help in fine-tuning operations to achieve higher efficiency.
Skill Development and Workforce Planning
Ensure that your workforce is well-trained and adaptable to new technologies and processes. Workforce planning tools integrated with your APS can forecast labor needs and help manage shifts and schedules effectively.
Regularly Review and Optimize Your Capacity Planning Strategies
Market conditions and technologies evolve, so should your capacity planning strategies. Regular reviews and updates to your planning processes ensure that your manufacturing operations remain competitive and responsive to changes.
Effective capacity planning is critical for the success of any packaging manufacturing facility. By integrating advanced planning solutions like PlanetTogether with major ERP, SCM, and MES systems, Plant Managers can not only enhance operational efficiency but also adapt swiftly to market demands. Adopting these best practices will ensure that your facility remains competitive, responsive, and agile in the ever-changing landscape of manufacturing.
Incorporating these strategies and leveraging technological integrations will position your manufacturing operations at the forefront of efficiency and innovation, driving substantial improvements in productivity and profitability.
Are you ready to take your manufacturing operations to the next level? Contact us today to learn more about how PlanetTogether can help you achieve your goals and drive success in your industry.
LEAVE A COMMENT