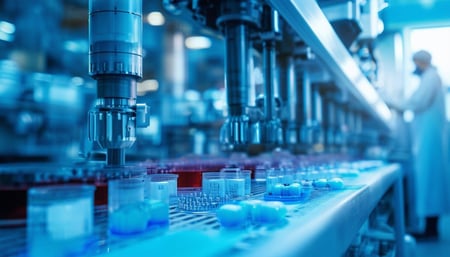
Business Strategy and Customer Demand
The demand for innovative medical devices and life-saving products grows as customers and healthcare providers seek reliable, high-quality solutions. Simultaneously, organizations must align their business strategies with customer demand to stay competitive while navigating market complexities.
In this landscape, integrating advanced planning tools like PlanetTogether with enterprise systems such as SAP, Oracle, Microsoft, Kinaxis, or Aveva offers a game-changing opportunity. It enables production planners to respond dynamically to market demands, optimize resource utilization, and drive alignment between strategic goals and customer needs.
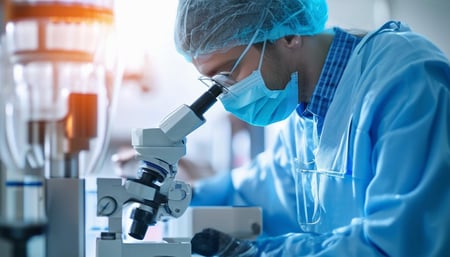
The Growing Complexity of Medical Manufacturing
Medical manufacturing operates in an environment of stringent regulatory requirements, diverse product portfolios, and fluctuating demand patterns. Several factors contribute to the complexity production planners face:
Regulatory Compliance: Medical products must adhere to strict quality standards, which can complicate production schedules and workflows.
Short Product Life Cycles: Rapid innovation in the medical field means products often have shorter lifespans, requiring agile production planning.
Customer-Centric Expectations: Healthcare providers demand tailored solutions and faster delivery times without compromising on quality.
Resource Optimization: Efficient use of equipment, materials, and labor is critical to maintaining profitability while meeting demand.
Addressing these challenges requires a comprehensive business strategy and tools that empower production planners with real-time visibility, predictive analytics, and seamless system integration.
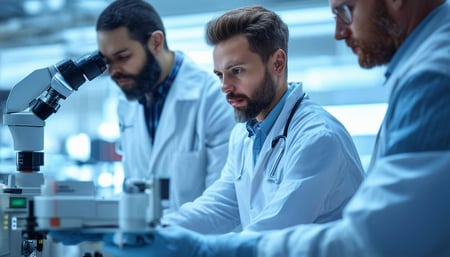
Aligning Business Strategy with Customer Demand
To effectively balance strategic goals with customer needs, production planners must address key elements of business strategy:
Demand Forecasting
Forecasting is the foundation of aligning production with market demand. Advanced integration between PlanetTogether and systems like Kinaxis or SAP enhances the accuracy of demand forecasts. By leveraging historical data, market trends, and predictive analytics, planners can make informed decisions about production volumes and schedules.
For instance, a demand spike for a new diagnostic device can be managed by adjusting production schedules in real-time. Integration with SAP's Advanced Planning and Optimization (APO) module allows seamless data flow between supply chain planning and shop floor execution, enabling immediate adjustments to meet demand without overproducing.
Agile Production Scheduling
Customer demand often fluctuates due to seasonal variations, market trends, or unforeseen events. Agile production scheduling allows planners to respond quickly to these changes. Tools like PlanetTogether, when integrated with Oracle Manufacturing Cloud, provide real-time visibility into production constraints, helping planners prioritize urgent orders and allocate resources efficiently.
For example, if a critical medical device order must be expedited, planners can adjust schedules, reallocate resources, and ensure timely delivery—all within a single integrated platform.
Resource Utilization and Capacity Planning
Optimal resource utilization is crucial to meeting demand while controlling costs. Integrating PlanetTogether with systems like Aveva's Unified Operations Center enables a holistic view of production assets. Planners can monitor machine availability, maintenance schedules, and workforce capacity to avoid bottlenecks and downtime.
This integration supports advanced capacity planning, ensuring that production lines remain flexible enough to handle high-mix, low-volume manufacturing—a common characteristic of medical manufacturing.

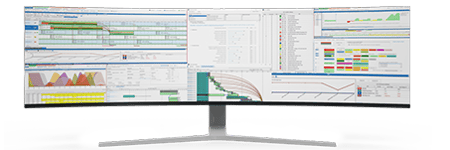
Benefits of System Integration in Production Planning
The integration of PlanetTogether with enterprise systems like SAP, Oracle, Microsoft, Kinaxis, or Aveva unlocks several benefits for production planners:
Enhanced Visibility and Transparency
Integrated systems provide a single source of truth for production data. Planners gain real-time insights into inventory levels, production progress, and order status, enabling proactive decision-making.
Improved Collaboration
With integrated platforms, cross-functional teams can collaborate more effectively. For example, procurement, production, and quality assurance teams can align their activities based on a unified production schedule, reducing miscommunication and errors.
Automation and Efficiency
Automation of routine planning tasks, such as order prioritization and schedule adjustments, frees up planners to focus on strategic activities. Integration with Microsoft Dynamics 365 can automate workflows, ensuring that production schedules are dynamically updated based on real-time data.
Scalability and Flexibility
As customer demand evolves, integrated systems provide the scalability needed to handle increased complexity. Whether it's a surge in orders for a new product or the introduction of additional production lines, tools like PlanetTogether can adapt to changing needs seamlessly.
Cost Savings and Sustainability
Efficient resource utilization minimizes waste and reduces production costs. Integration with platforms like Kinaxis RapidResponse helps planners simulate various production scenarios to identify the most cost-effective and sustainable options.
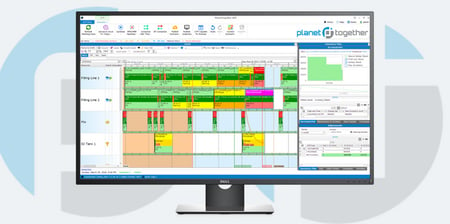
The Role of Data Analytics in Strategic Planning
Data analytics plays a pivotal role in aligning business strategy with customer demand. Integrated platforms like PlanetTogether provide actionable insights into production trends, resource utilization, and demand patterns. This data empowers planners to:
Identify and mitigate production bottlenecks.
Forecast demand with higher accuracy.
Optimize production schedules to maximize throughput.
For example, by analyzing production data from Oracle Cloud, planners can identify underutilized resources and redistribute workloads, ensuring efficient operations.
Key Considerations for Implementation
When integrating planning tools with enterprise systems, consider the following:
Stakeholder Alignment: Ensure that all relevant teams, including IT, production, and supply chain, are aligned on integration goals.
Scalability: Choose systems that can grow with your business needs, accommodating future expansions or product line additions.
Training and Support: Provide adequate training for planners and other users to ensure smooth adoption of the integrated platform.
Compliance and Security: Verify that the integration complies with industry regulations, such as FDA and ISO standards, and prioritize data security.
In medical manufacturing, aligning business strategy with customer demand is critical for maintaining competitiveness and delivering exceptional value. Production planners play a central role in this alignment, leveraging advanced tools and integrated systems to balance efficiency, flexibility, and quality.
The integration of PlanetTogether with ERP system platforms like SAP, Oracle, Microsoft, Kinaxis, or Aveva empowers planners with the insights, agility, and automation needed to navigate complexity and respond to market demands effectively. By embracing these technologies, medical manufacturing facilities can enhance their production capabilities, achieve strategic goals, and exceed customer expectations.
Are you ready to take your manufacturing operations to the next level? Contact us today to learn more about how PlanetTogether can help you achieve your goals and drive success in your industry.