Building Resilient Manufacturing Ecosystems
In industrial manufacturing, the pursuit of resilience has emerged as a vital goal. As global supply chains face unprecedented challenges, from pandemics to geopolitical tensions, manufacturers are seeking strategies to fortify their operations against disruptions.
One key avenue toward achieving resilience lies in the integration of advanced planning and scheduling (APS) solutions like PlanetTogether with Enterprise Resource Planning (ERP), Supply Chain Management (SCM), and Manufacturing Execution Systems (MES).
In this blog, we'll look into the concept of resilient manufacturing ecosystems and explore how integration can empower manufacturers to thrive in an ever-changing environment.
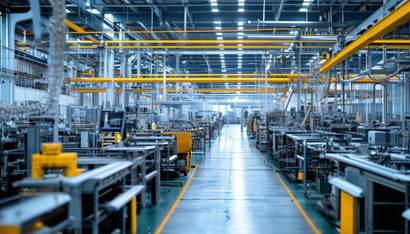
Resilient Manufacturing Ecosystems
Resilience in manufacturing refers to the ability of an organization to anticipate, adapt to, and recover from disruptions while maintaining core operations and customer satisfaction. Building a resilient manufacturing ecosystem entails fostering agility, visibility, and collaboration across the entire value chain.
Agility enables manufacturers to swiftly respond to changes in demand, supply, and production conditions. Visibility provides real-time insights into the status of operations, inventory levels, and external factors that may impact the supply chain. Collaboration facilitates seamless communication and coordination among internal departments, suppliers, and partners.
-Apr-01-2024-01-39-55-8668-PM.png?width=300&height=48&name=logo%20(2)-Apr-01-2024-01-39-55-8668-PM.png)
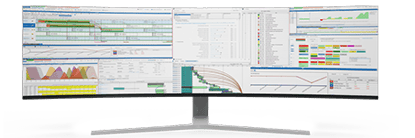
The Role of Advanced Planning and Scheduling (APS) Solutions
At the heart of resilient manufacturing ecosystems lies advanced planning and scheduling (APS) software. These sophisticated tools leverage algorithms and optimization techniques to generate optimal production plans, schedules, and resource allocations.
One leading APS solution, PlanetTogether, empowers manufacturers to optimize their production processes, maximize resource utilization, and minimize lead times. With features such as constraint-based scheduling, what-if scenario analysis, and capacity planning, PlanetTogether enables manufacturers to achieve operational excellence and meet customer demands efficiently.
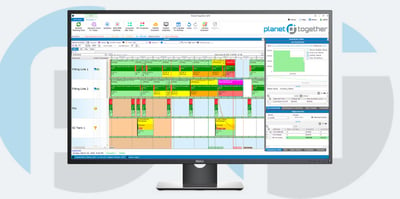
The Power of Integration
While APS solutions like PlanetTogether offer robust capabilities for production planning and scheduling, their full potential is unlocked through integration with ERP, SCM, and MES systems. Integration enables seamless data exchange and synchronization across disparate systems, ensuring a unified and holistic approach to manufacturing operations.
Let's explore how integration between PlanetTogether and leading ERP, SCM, and MES platforms enhances the resilience of manufacturing ecosystems:
Integration with SAP
SAP is one of the most widely used ERP systems in the manufacturing industry. By integrating PlanetTogether with SAP, manufacturers can leverage real-time data exchange between production planning and enterprise resource management. This integration streamlines order fulfillment, inventory management, and resource allocation, enabling manufacturers to respond rapidly to changes in demand and supply.
Integration with Oracle
Oracle offers comprehensive SCM and MES solutions that complement PlanetTogether's APS capabilities. Integrating PlanetTogether with Oracle systems facilitates end-to-end visibility and control over manufacturing operations. Manufacturers can synchronize production plans with procurement, quality management, and shop floor execution, optimizing efficiency and minimizing disruptions.
Integration with Microsoft Dynamics
Microsoft Dynamics provides a flexible and scalable ERP platform for manufacturing organizations. By integrating PlanetTogether with Microsoft Dynamics, manufacturers can enhance agility and responsiveness throughout the supply chain. Seamless data exchange between production planning and ERP modules enables synchronized demand forecasting, inventory optimization, and production scheduling.
Integration with Kinaxis
Kinaxis offers a cloud-based SCM platform that enables real-time collaboration and decision-making. Integrating PlanetTogether with Kinaxis allows manufacturers to achieve supply chain orchestration and resilience. By aligning production plans with demand signals and supply constraints, manufacturers can optimize inventory levels, reduce lead times, and mitigate supply chain risks.
Integration with Aveva
Aveva provides MES solutions that enable digital transformation and operational excellence. Integrating PlanetTogether with Aveva MES enhances visibility and control over shop floor operations. Real-time data exchange between production scheduling and execution systems enables manufacturers to optimize resource utilization, track production progress, and ensure compliance with quality standards.
In an era defined by volatility and uncertainty, resilience has become a strategic imperative for manufacturers. By building resilient manufacturing ecosystems powered by integration between PlanetTogether and ERP, SCM, and MES systems, manufacturers can adapt to changing market conditions, mitigate risks, and seize opportunities for growth.
As the manufacturing landscape continues to evolve, the path to resilience lies in harnessing the full potential of advanced planning and scheduling solutions like PlanetTogether and integrating them seamlessly with enterprise systems. By embracing integration, manufacturers can future-proof their operations and thrive in an increasingly complex and interconnected world.
Are you ready to take your manufacturing operations to the next level? Contact us today to learn more about how PlanetTogether can help you achieve your goals and drive success in your industry.
LEAVE A COMMENT