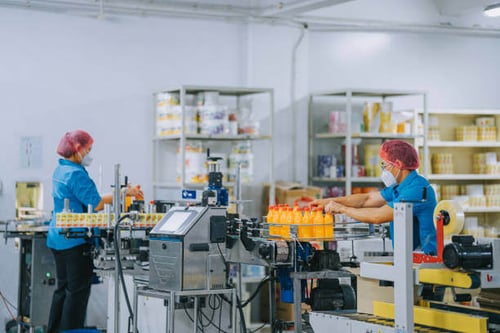
How Active Packaging & Smart Manufacturing Are Reshaping Manufacturing Operations
The packaging industry is undergoing a transformative shift, driven by consumer demand for safer, fresher, and more sustainable products. Active packaging—a revolutionary concept that extends shelf life, enhances food safety, and improves product quality—has emerged as a key differentiator for manufacturers. For plant managers in packaging and container manufacturing facilities, integrating active packaging solutions is no longer an option but a must to remain competitive in a rapidly evolving market.
However, successfully implementing active packaging involves more than just material innovations. It requires precise production planning, supply chain coordination, and seamless integration of manufacturing execution systems (MES) with enterprise resource planning (ERP) solutions like SAP, Oracle, Microsoft, Kinaxis, or Aveva. This is where advanced planning and scheduling (APS) software like PlanetTogether can revolutionize operations, ensuring efficiency, compliance, and profitability.
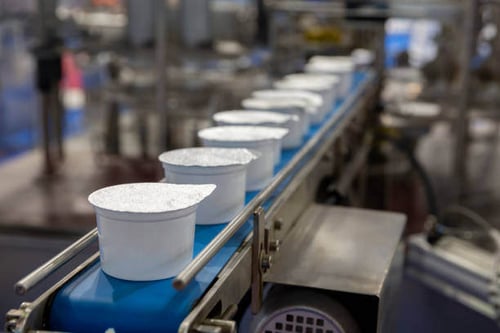
What is Active Packaging?
Active packaging incorporates components that actively interact with the packaged product to extend shelf life, maintain quality, and enhance consumer safety. Unlike traditional packaging, which merely acts as a passive barrier, active packaging can:
Absorb oxygen, ethylene, or moisture to slow spoilage.
Release antimicrobial agents to reduce contamination.
Incorporate temperature-sensitive indicators for supply chain monitoring.
Use nanotechnology to improve barrier properties and recyclability.
With industries such as food, pharmaceuticals, and medical manufacturing increasingly demanding these features, plant managers in packaging and container manufacturing must adapt their operations to accommodate the new materials, production methods, and regulatory requirements associated with active packaging.
Challenges in Active Packaging Manufacturing
Complexity in Production Scheduling
Manufacturing active packaging requires precise material handling, temperature control, and production sequencing. Without advanced scheduling tools, plants may experience bottlenecks, inefficient machine utilization, and increased downtime.
Supply Chain Disruptions
Active packaging materials often include specialized additives, coatings, or embedded technologies, which may have limited supplier availability. Unpredictable lead times can disrupt production schedules, making agile planning crucial.
Regulatory Compliance
Industries such as food and pharmaceuticals have stringent regulatory standards regarding active packaging safety and effectiveness. Compliance with FDA, EFSA, and other regulatory bodies demands rigorous tracking, traceability, and documentation throughout the production process.
Integration with Existing Systems
Many packaging facilities operate on legacy ERP and MES systems that are not designed to handle the complexities of active packaging production. Integrating new processes into existing workflows without causing disruptions is a significant challenge.
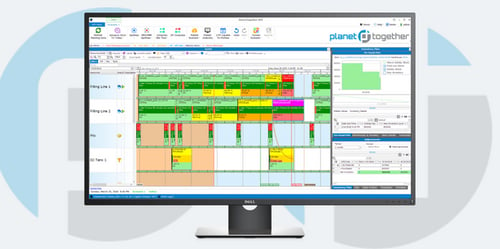
How PlanetTogether APS Solves These Challenges
To address these challenges, integrating PlanetTogether APS with leading ERP solutions such as SAP, Oracle, Microsoft, Kinaxis, and Aveva allows plant managers to optimize production planning and scheduling, improve supply chain visibility, and ensure regulatory compliance. Here’s how:
Enhanced Production Scheduling & Resource Optimization
PlanetTogether provides dynamic scheduling capabilities that allow plant managers to:
Optimize machine utilization by sequencing production runs efficiently.
Reduce changeover times between different active packaging types.
Minimize waste by synchronizing raw material availability with production schedules.
By integrating PlanetTogether with ERP systems like SAP or Oracle, real-time production data can be used to dynamically adjust schedules based on demand fluctuations and supply chain constraints.
Agile Supply Chain Planning & Inventory Management
By leveraging integration with Kinaxis or Aveva, manufacturers can:
Gain end-to-end supply chain visibility to anticipate material shortages.
Automate procurement based on real-time production data and demand forecasts.
Reduce inventory costs while maintaining a buffer for unexpected disruptions.
This level of agility is particularly crucial for active packaging, where specialized materials often require longer lead times and precise inventory control.
Ensuring Compliance & Traceability
PlanetTogether’s integration with MES and ERP systems allows plant managers to:
Track batch-level production data for full traceability.
Automate compliance reporting for regulatory audits.
Implement real-time quality control measures to meet industry standards.
For pharmaceutical packaging, for example, integration with Microsoft Dynamics 365 can enable real-time monitoring of temperature-sensitive packaging components, ensuring compliance with strict FDA regulations.
Seamless ERP & MES Integration for Smart Manufacturing
Many packaging facilities operate hybrid IT landscapes where multiple systems (e.g., SAP ERP for enterprise management, Oracle MES for shop floor execution) coexist. PlanetTogether bridges the gap between these systems, allowing:
Data synchronization across production, inventory, and procurement teams.
AI-driven predictive maintenance to reduce equipment downtime.
Real-time visibility into KPIs for improved decision-making.
Active packaging is no longer just a trend—it’s the future of the packaging industry. For plant managers in packaging and container manufacturing facilities, the integration of PlanetTogether with leading ERP and MES solutions ensures that this future is efficient, cost-effective, and compliant. Investing in advanced planning and scheduling solutions today will pave the way for a smarter, more agile manufacturing operation tomorrow.
Are you ready to transform your packaging facility with active packaging solutions? Contact us today to learn more about how PlanetTogether can optimize your production planning and ERP integration for a seamless transition.
LEAVE A COMMENT