AI-Powered Predictive Scheduling for Dynamic Material Availability
Operations Directors face a multitude of challenges in chemical manufacturing. From fluctuating material availability to complex production schedules, the need for efficient and agile processes has never been greater.
In this blog, we look into the realm of AI-powered predictive scheduling, exploring how it can revolutionize operations in chemical manufacturing facilities, particularly when integrated with leading ERP, SCM, and MES systems like SAP, Oracle, Microsoft, Kinaxis, Aveva, and others.
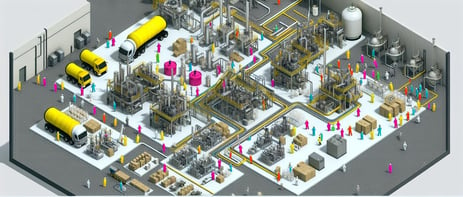
The Complexity of Material Availability in Chemical Manufacturing
Chemical manufacturing is inherently complex, with numerous variables impacting production schedules. One of the most critical factors is material availability. Whether it's raw materials, intermediates, or finished products, any disruption in the supply chain can have cascading effects on production timelines, customer satisfaction, and ultimately, the bottom line.
Traditionally, scheduling in chemical manufacturing has been reactive, relying on historical data and manual adjustments to accommodate unforeseen disruptions. However, this approach is no longer sufficient in today's dynamic business environment, where agility and foresight are paramount.
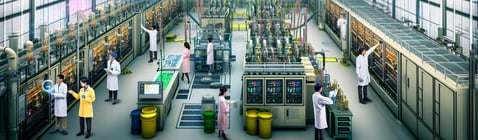
Enter AI-Powered Predictive Scheduling
AI-powered predictive scheduling represents a paradigm shift in how manufacturing facilities approach production planning. By leveraging advanced algorithms and machine learning techniques, predictive scheduling software can analyze vast amounts of data in real-time to forecast material availability and optimize production schedules accordingly.
At the heart of predictive scheduling is the ability to anticipate potential bottlenecks and proactively adjust schedules to mitigate risks. This proactive approach not only minimizes the impact of disruptions but also maximizes resource utilization and overall efficiency.
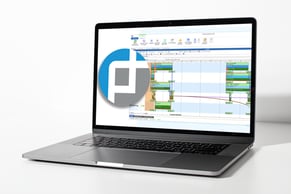
Integration with ERP, SCM, and MES Systems
While predictive scheduling holds tremendous potential on its own, its true power is unlocked when integrated with existing ERP, SCM, and MES systems. Integration allows for seamless data exchange between different systems, enabling a holistic view of operations and enhancing decision-making capabilities.
Leading ERP systems like SAP, Oracle, Microsoft Dynamics, and MES platforms like Aveva and Kinaxis provide a wealth of data related to inventory levels, production orders, and supply chain dynamics. By integrating predictive scheduling with these systems, Operations Directors gain access to real-time insights that enable them to make informed decisions and optimize production schedules on the fly.
Benefits of Integration
The integration between predictive scheduling software and ERP, SCM, and MES systems offers a myriad of benefits for chemical manufacturing facilities:
Real-Time Visibility
Integration provides real-time visibility into all aspects of the manufacturing process, from raw material procurement to final product delivery. This visibility allows Operations Directors to identify potential bottlenecks and resource constraints before they escalate, enabling proactive intervention to maintain production schedules.
Enhanced Decision-Making
By leveraging data from ERP, SCM, and MES systems, predictive scheduling software can generate accurate forecasts and predictive analytics. These insights empower Operations Directors to make data-driven decisions that optimize production efficiency, minimize costs, and maximize profitability.
Improved Collaboration
Integration fosters collaboration between different departments within the organization, breaking down silos and enabling cross-functional coordination. With access to real-time data and insights, teams can align their efforts to achieve common objectives, such as reducing lead times, improving on-time delivery, and enhancing customer satisfaction.
Adaptive Planning
Predictive scheduling software continuously analyzes incoming data to adapt production schedules in response to changing conditions. Whether it's a sudden increase in demand, a supplier delay, or a machine breakdown, the system can automatically reoptimize schedules to minimize disruptions and maintain operational efficiency.
Scalability and Flexibility
Integration with ERP, SCM, and MES systems provides scalability and flexibility to accommodate growth and adapt to evolving business requirements. Whether expanding production capacity, introducing new product lines, or entering new markets, predictive scheduling software can scale seamlessly to meet the changing needs of the organization.
-May-08-2024-04-36-12-8483-PM.png?width=300&height=48&name=logo%20(2)-May-08-2024-04-36-12-8483-PM.png)
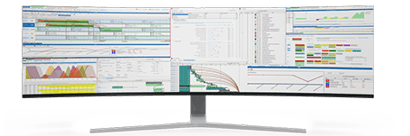
PlanetTogether Integration
One notable example of predictive scheduling software is PlanetTogether, a leading provider of advanced planning and scheduling solutions. PlanetTogether's AI-powered platform offers robust capabilities for optimizing production schedules based on real-time data and predictive analytics.
When integrated with ERP, SCM, and MES systems such as SAP, Oracle, Microsoft Dynamics, Kinaxis, and Aveva, PlanetTogether enables chemical manufacturing facilities to achieve unprecedented levels of efficiency and agility.
Consider a scenario where a chemical manufacturing facility experiences a sudden increase in demand for a key product due to market dynamics. With PlanetTogether integrated with SAP, the system can automatically adjust production schedules to prioritize the production of the in-demand product while optimizing resource allocation across the facility.
PlanetTogether's predictive capabilities enable Operations Directors to anticipate potential supply chain disruptions, such as raw material shortages or transportation delays, and take preemptive actions to mitigate risks. By leveraging real-time data from ERP, SCM, and MES systems, the system can generate accurate forecasts and predictive analytics that inform proactive decision-making and ensure uninterrupted production.
The integration between PlanetTogether and leading ERP, SCM, and MES systems empowers Operations Directors in chemical manufacturing facilities to optimize production schedules, minimize disruptions, and maximize efficiency. By harnessing the power of AI and predictive analytics, organizations can stay ahead of the curve in today's competitive landscape, delivering superior products and services to customers while driving sustainable growth and profitability.
As the demands of chemical manufacturing continue to evolve, Operations Directors must embrace innovative technologies that enable them to navigate complexity and uncertainty with confidence. AI-powered predictive scheduling such as PlanetTogether, when integrated with ERP, SCM, and MES systems, represents a game-changer for the industry, offering unprecedented levels of efficiency, agility, and resilience.
By leveraging real-time data, predictive analytics, and advanced algorithms, predictive scheduling software empowers Operations Directors to optimize production schedules, anticipate supply chain disruptions, and make informed decisions that drive business success. With the right tools and strategies in place, chemical manufacturing facilities can thrive in today's dynamic environment, delivering value to customers, stakeholders, and the bottom line alike.
Are you ready to take your manufacturing operations to the next level? Contact us today to learn more about how PlanetTogether can help you achieve your goals and drive success in your industry.