AI-Enhanced Predictive Maintenance Resource Allocation
In the highly competitive and rapidly evolving chemical manufacturing industry, the role of a Production Scheduler is more crucial than ever. The efficient allocation of resources, the optimization of production processes, and the ability to adapt to changing market demands are paramount for success. To achieve these goals, manufacturers are increasingly turning to advanced technologies, such as AI-enhanced predictive maintenance, to ensure their operations run smoothly.
In this blog, we will explore the integration of AI-driven predictive maintenance with production scheduling systems like PlanetTogether and major ERP, SCM, and MES platforms, including SAP, Oracle, Microsoft, Kinaxis, and Aveva.
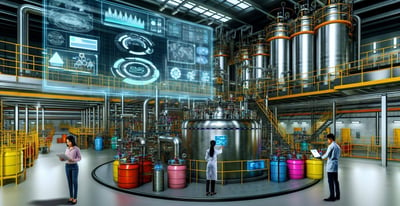
Predictive Maintenance in Chemical Manufacturing
Predictive maintenance has emerged as a game-changer in the manufacturing industry, including chemical manufacturing. It involves the use of data analytics, machine learning, and artificial intelligence to predict when equipment is likely to fail, allowing for timely maintenance and preventing costly unplanned downtime. However, implementing predictive maintenance effectively in a chemical manufacturing facility comes with its own set of challenges:
Data Integration: Chemical manufacturing facilities generate vast amounts of data from sensors, equipment, and processes. Integrating this data with production scheduling systems and ERP platforms can be a complex and daunting task.
Algorithm Selection: Choosing the right predictive maintenance algorithm and fine-tuning it for specific equipment and processes is critical. It requires a deep understanding of both maintenance and production scheduling.
Resource Allocation: Predictive maintenance generates insights into when maintenance should be performed, but the allocation of resources (labor, materials, tools) at the right time is crucial to ensure minimal disruption to production schedules.
Integration with Existing Systems: Many chemical manufacturers already have established production scheduling systems and ERP platforms in place. Integrating AI-driven predictive maintenance solutions with these systems is essential for a seamless workflow.

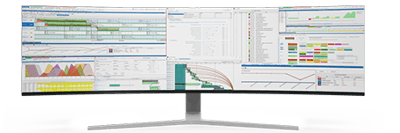
AI-Enhanced Predictive Maintenance and PlanetTogether
PlanetTogether is a widely used production scheduling software known for its robust features in optimizing production processes. Integrating AI-enhanced predictive maintenance with PlanetTogether can bring about a revolution in resource allocation and production planning.
Real-time Data Integration: AI-driven predictive maintenance systems can collect and analyze real-time data from sensors and equipment, making it easier to identify when maintenance is needed. This data can seamlessly integrate with PlanetTogether, allowing for immediate adjustments to production schedules when maintenance is scheduled.
Preventive Scheduling: With predictive maintenance insights integrated into PlanetTogether, Production Schedulers can proactively schedule maintenance during planned downtime periods, minimizing production disruptions.
Resource Allocation: Predictive maintenance systems can provide recommendations on the allocation of resources needed for maintenance tasks. Production Schedulers can use this information to ensure that the right personnel, materials, and tools are available when maintenance is scheduled.
Improved Planning: The integration of predictive maintenance with PlanetTogether allows for more accurate long-term production planning. Schedulers can factor in maintenance needs and optimize production schedules accordingly.
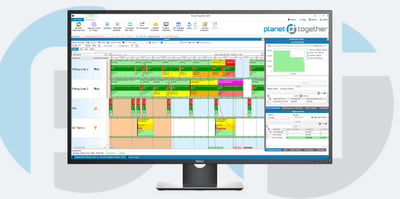
AI-Enhanced Predictive Maintenance and ERP, SCM, and MES Systems
In addition to PlanetTogether, chemical manufacturers often rely on ERP, SCM, and MES systems from major vendors like SAP, Oracle, Microsoft, Kinaxis, and Aveva. Integrating AI-enhanced predictive maintenance with these systems offers several advantages:
Seamless Data Flow: AI-driven predictive maintenance systems can seamlessly exchange data with ERP, SCM, and MES platforms, ensuring that maintenance schedules are aligned with overall business goals and resource availability.
Inventory Optimization: Predictive maintenance can help reduce inventory costs by ensuring that maintenance activities are scheduled to coincide with the availability of critical spare parts.
Demand Forecasting: By analyzing equipment performance and maintenance needs, predictive maintenance can provide valuable insights for demand forecasting, helping manufacturers meet market demands more efficiently.
Compliance and Reporting: Integration with ERP systems facilitates compliance with regulatory requirements, as maintenance records can be automatically generated and stored in a centralized database.
Continuous Improvement: The data generated by predictive maintenance can be used for continuous improvement initiatives, helping chemical manufacturers refine their processes and reduce costs.
Selecting the Right AI-Enhanced Predictive Maintenance Solution
Choosing the right AI-enhanced predictive maintenance solution is a crucial step for chemical manufacturers. Here are some factors to consider:
Compatibility: Ensure that the predictive maintenance solution you select is compatible with your existing production scheduling system and ERP, SCM, and MES platforms.
Customization: Look for a solution that can be customized to the unique needs of your chemical manufacturing facility, including specific equipment and processes.
Scalability: Consider whether the solution can scale with your business as it grows and adapts to changing requirements.
Integration Expertise: Work with vendors or consultants who have expertise in integrating AI-driven predictive maintenance with production scheduling and ERP systems.
Data Security: Ensure that the solution adheres to industry standards for data security and compliance, especially when dealing with sensitive data in chemical manufacturing.
ROI Analysis: Conduct a thorough analysis to understand the potential return on investment (ROI) that the predictive maintenance solution can deliver in terms of reduced downtime, improved resource allocation, and cost savings.
In chemical manufacturing, AI-enhanced predictive maintenance offers a powerful solution for optimizing resource allocation and production scheduling. Integrating predictive maintenance with production scheduling systems like PlanetTogether and major ERP, SCM, and MES platforms can lead to increased efficiency, reduced downtime, and improved competitiveness.
As a Production Scheduler, embracing these technologies and working closely with experts in the field will be key to staying ahead in the ever-evolving chemical manufacturing landscape. By harnessing the power of AI and predictive maintenance, you can ensure that your facility runs smoothly and efficiently, meeting market demands while minimizing disruptions.
Are you ready to take your manufacturing operations to the next level? Contact us today to learn more about how PlanetTogether and integrated scheduling solutions can help you achieve your sustainability goals and drive success in the chemical industry.
LEAVE A COMMENT