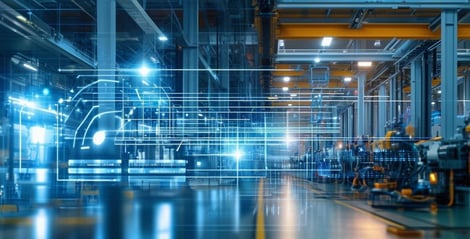
AI-Enabled Optimization Algorithms for Minimizing Downtime in Industrial Manufacturing
In the competitive world of industrial manufacturing, even minor inefficiencies can lead to significant losses. Production planners are often tasked with balancing a myriad of variables—including machine utilization, workforce allocation, and inventory management—to achieve optimal operational efficiency.
One of the most persistent challenges they face is minimizing downtime. Fortunately, advancements in artificial intelligence (AI) and its integration with planning software like PlanetTogether and ERP systems such as SAP, Oracle, Microsoft, Kinaxis, or Aveva have brought new possibilities for tackling this issue.
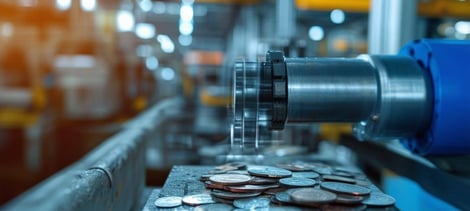
The Cost of Downtime
Downtime in manufacturing can result from a variety of causes: machine breakdowns, supply chain disruptions, labor shortages, or inefficient scheduling. Studies estimate that manufacturing downtime costs industrial facilities billions of dollars annually. Beyond the financial implications, frequent or prolonged downtime can disrupt production schedules, delay customer deliveries, and damage a company’s reputation.
Minimizing downtime is no longer just about reactive maintenance or basic optimization techniques. With AI-enabled optimization algorithms, production planners have a powerful tool to proactively address inefficiencies, identify bottlenecks, and create adaptive schedules that can respond to real-time changes.
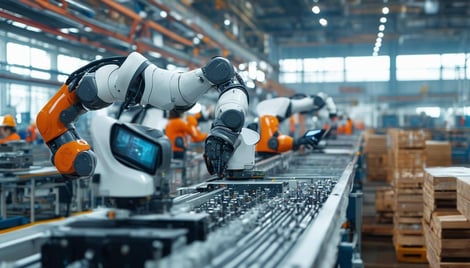
What Are AI-Enabled Optimization Algorithms?
AI-enabled optimization algorithms are advanced computational tools designed to solve complex problems by mimicking human intelligence. These algorithms analyze vast amounts of data, identify patterns, and make data-driven decisions faster and more accurately than traditional methods. In the context of production planning, these algorithms can:
Predict machine failures through predictive maintenance.
Optimize production schedules to reduce idle time.
Identify inefficiencies in resource allocation.
Simulate various scenarios to prepare for unexpected disruptions.
When integrated with systems like PlanetTogether and ERP solutions such as SAP or Microsoft Dynamics, these algorithms can provide a seamless flow of data across the manufacturing ecosystem, enhancing their effectiveness.
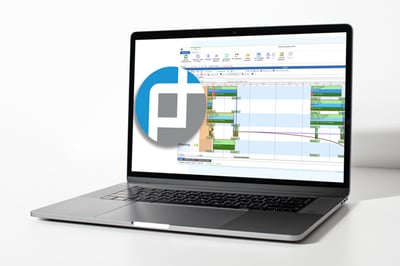
Integration of PlanetTogether with Leading ERP Systems
One of the most significant advantages of AI-enabled optimization algorithms is their ability to work within integrated environments. PlanetTogether, a leading advanced planning and scheduling (APS) software, excels in creating dynamic and responsive schedules. When connected to ERP systems like SAP, Oracle, or Kinaxis, the integration enables real-time data sharing and enhanced decision-making.
For example, a production planner using PlanetTogether integrated with SAP S/4HANA can:
Access Real-Time Data: Gain insights into inventory levels, machine availability, and workforce schedules directly from the ERP system.
Enhance Predictive Maintenance: AI algorithms can analyze data from sensors and maintenance logs stored in SAP, helping predict and prevent equipment failures before they occur.
Optimize Material Flow: With real-time inventory data from SAP, PlanetTogether’s optimization algorithms can adjust production schedules to ensure materials are available precisely when needed, minimizing idle time.
Scenario Planning: Simulate various scheduling scenarios to assess the impact of unexpected events, such as supply chain delays or equipment failures, and create contingency plans.
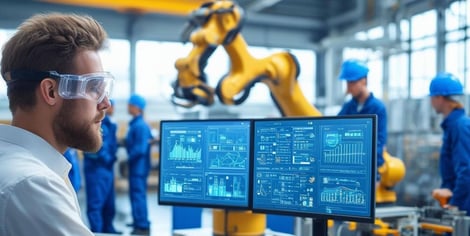
Applications of AI-Enabled Optimization in Industrial Manufacturing
AI-enabled optimization algorithms bring several key applications to industrial manufacturing facilities:
Dynamic Scheduling
Traditional scheduling methods often struggle to adapt to changes in real time. AI algorithms can process large datasets—including machine availability, workforce shifts, and production targets—to create dynamic schedules that adapt to changes as they occur. For example, if a machine unexpectedly goes offline, the algorithm can instantly adjust the schedule to redistribute tasks, minimizing delays.
Predictive Maintenance
Unplanned equipment failures are one of the leading causes of downtime. AI algorithms analyze historical performance data and sensor inputs to predict when machines are likely to fail. By scheduling maintenance proactively, production planners can reduce unexpected downtime and extend the lifespan of critical equipment.
Bottleneck Identification
AI algorithms can pinpoint bottlenecks in the production process by analyzing throughput data and identifying stages where delays frequently occur. Addressing these bottlenecks—whether by reallocating resources or adjusting workflows—can significantly improve overall efficiency.
Inventory Optimization
Maintaining the right balance of inventory is critical for minimizing downtime. AI-enabled systems integrated with ERP platforms like Oracle NetSuite or Microsoft Dynamics 365 can monitor inventory levels in real time, ensuring that raw materials are always available when needed while avoiding overstocking.
Energy Efficiency
Energy consumption is another area where AI can drive optimization. By analyzing energy usage patterns, AI algorithms can recommend scheduling adjustments to reduce peak energy usage, lowering costs and minimizing environmental impact.
Minimizing downtime is a critical priority for production planners in industrial manufacturing facilities. AI-enabled optimization algorithms, combined with tools like PlanetTogether and integrated ERP systems, offer a transformative solution. By leveraging these technologies, production planners can create adaptive schedules, predict and prevent disruptions, and achieve unprecedented levels of efficiency.
The future of manufacturing is intelligent, connected, and dynamic. For production planners willing to embrace AI-enabled optimization, the opportunities are endless—and the rewards are significant.
Are you ready to take your manufacturing operations to the next level? Contact us today to learn more about how PlanetTogether can help you achieve your goals and drive success in your industry.