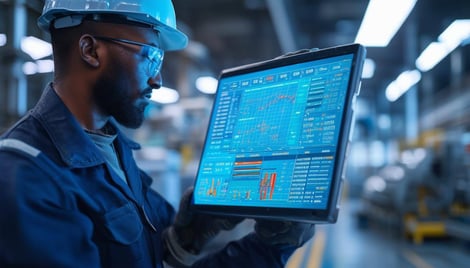
AI-Driven Root Cause Analysis to Improve Schedule Adherence in Industrial Manufacturing
Maintaining schedule adherence is critical to meeting customer demands, optimizing resource utilization, and ensuring profitability. Yet, persistent disruptions—machine breakdowns, supply chain delays, or unexpected quality issues—can derail even the most meticulously planned schedules.
Addressing these challenges requires more than traditional problem-solving; it necessitates the adoption of advanced technologies such as AI-driven root cause analysis integrated with robust planning systems like PlanetTogether and enterprise platforms such as SAP, Oracle, Microsoft, Kinaxis, or Aveva.
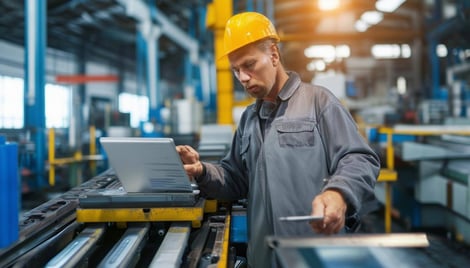
The Challenge of Schedule Adherence
Schedule adherence measures the degree to which actual production aligns with planned schedules. High adherence rates indicate efficient operations and effective resource management, while low adherence signals potential inefficiencies, such as bottlenecks, resource constraints, or unexpected downtimes. Identifying and resolving these issues quickly is crucial for staying competitive, yet traditional diagnostic methods often fall short in uncovering complex, multi-factorial problems.
Common obstacles to schedule adherence include:
Equipment Failures: Downtime due to unexpected breakdowns or maintenance issues.
Supply Chain Disruptions: Delays in receiving raw materials or components.
Labor Shortages: Absenteeism or lack of skilled personnel impacting production timelines.
Quality Issues: Rework or scrap caused by deviations in production quality.
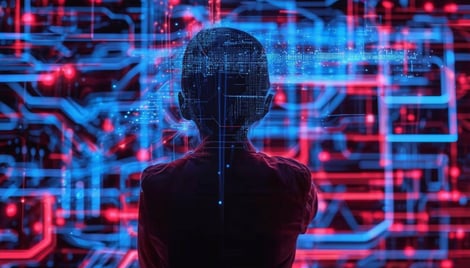
Enter AI-Driven Root Cause Analysis
Artificial Intelligence (AI) has revolutionized problem-solving in manufacturing by enabling rapid and accurate identification of root causes. AI-driven root cause analysis uses machine learning (ML), data analytics, and predictive modeling to uncover hidden patterns, correlations, and anomalies in production data. This approach not only identifies the underlying issues but also suggests actionable solutions to prevent recurrence.
Key features of AI-driven root cause analysis include:
Data Integration: AI algorithms analyze data from multiple sources, including production logs, IoT sensors, supply chain systems, and ERP platforms like SAP or Oracle.
Real-Time Insights: Continuous monitoring and analysis provide real-time insights into potential issues.
Predictive Capabilities: Advanced ML models predict future disruptions based on historical data and trends.
Scalability: AI systems can adapt to diverse manufacturing environments and scales, from single plants to global operations.
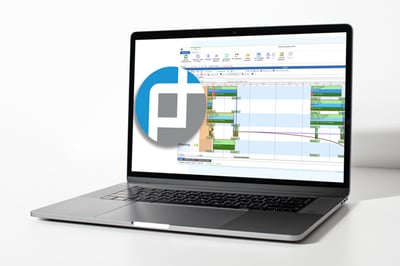
Integration with PlanetTogether and ERP Systems
For Manufacturing IT Managers, integrating AI-driven root cause analysis with advanced planning systems like PlanetTogether and ERP platforms such as Microsoft Dynamics, SAP, Oracle, Kinaxis, or Aveva offers unparalleled benefits. These integrations create a cohesive ecosystem where planning, execution, and diagnostics operate seamlessly.
Benefits of Integration:
Unified Data Streams: Integration consolidates data from production schedules, inventory levels, machine performance, and supply chain operations, enabling comprehensive analysis.
Automated Feedback Loops: Identified root causes and recommended solutions feed directly into planning systems, ensuring schedules are updated in real time.
Enhanced Collaboration: Integration fosters better communication across departments, aligning IT, operations, and production teams around shared goals.
Proactive Problem-Solving: Predictive insights allow planners to address potential issues before they impact schedules.
For example, integrating PlanetTogether with SAP’s ERP system ensures that production schedules are dynamically adjusted based on real-time insights from AI-driven root cause analysis. If a machine breakdown is detected, the integration automatically reschedules jobs, reallocates resources, and updates supply chain requirements to minimize disruptions.
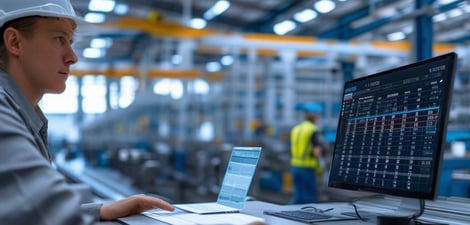
How AI Improves Schedule Adherence
AI-driven root cause analysis impacts schedule adherence in several transformative ways:
Rapid Problem Identification
AI systems analyze vast amounts of production data in seconds, identifying anomalies that traditional methods might overlook. For instance, a sudden spike in machine vibration data from IoT sensors might indicate impending failure. By identifying this anomaly early, AI prevents unplanned downtime and keeps schedules on track.
Predictive Maintenance
Integrating predictive maintenance with scheduling platforms ensures that maintenance activities are planned during non-peak hours. AI algorithms predict when equipment is likely to fail, enabling planners to schedule repairs without disrupting production.
Supply Chain Optimization
AI-driven analysis identifies patterns and trends in supply chain data, such as recurring delays from a specific supplier. By addressing these root causes, manufacturers can improve material availability and maintain production schedules.
Quality Management
AI models analyze quality control data to identify factors contributing to defects. This information feeds back into production schedules, prioritizing jobs with the highest likelihood of success and reducing rework or scrap-related delays.
Enhanced Decision-Making
AI-powered dashboards and visualizations provide IT managers and planners with actionable insights. For instance, integration between PlanetTogether and Kinaxis allows for real-time simulation of schedule changes, enabling teams to assess the impact of different scenarios before implementation.
As industrial manufacturing becomes increasingly complex, the role of advanced technologies like AI-driven root cause analysis will continue to grow. By integrating these capabilities with planning systems like PlanetTogether and enterprise platforms such as SAP, Oracle, Microsoft, Kinaxis, or Aveva, Manufacturing IT Managers can achieve unparalleled efficiency and reliability.
Embracing AI is not just a technological upgrade; it’s a strategic imperative for manufacturers aiming to stay competitive in a dynamic market. With AI-driven insights, your facility can move from reactive problem-solving to proactive optimization, setting a new standard for schedule adherence and operational excellence.
Are you ready to take your manufacturing operations to the next level? Contact us today to learn more about how PlanetTogether can help you achieve your goals and drive success in your industry.