AI-Driven Optimization of Procurement Lead Time Variability
As a Purchasing Manager, you understand the challenges of dealing with lead time variability, supplier reliability, and the ever-present pressure to streamline operations. Fortunately, advancements in artificial intelligence (AI) and software integration are revolutionizing the way procurement is managed, paving the way for enhanced efficiency and cost-effectiveness.
In this blog, we look into the realm of AI-driven optimization of procurement lead time variability and explore how integration between PlanetTogether and leading ERP, SCM, and MES systems such as SAP, Oracle, Microsoft, Kinaxis, and Aveva is reshaping the landscape of food and beverage manufacturing.
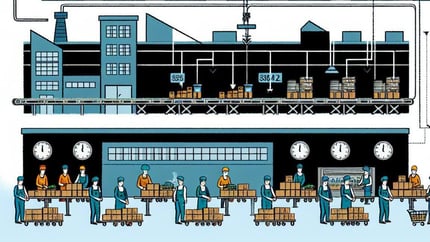
Understanding Procurement Lead Time Variability
Procurement lead time variability refers to the fluctuation in the time it takes to receive goods from suppliers. In the food and beverage industry, where freshness and quality are paramount, managing lead times effectively is crucial to avoid stockouts, minimize excess inventory, and ensure timely production.
Traditional procurement methods often struggle to cope with lead time variability, relying on manual forecasting and reactive approaches that leave room for error. However, with the advent of AI-powered solutions, companies can now harness the power of data analytics and predictive algorithms to optimize procurement processes like never before.
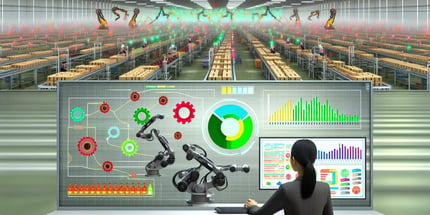
The Role of AI in Procurement Optimization
AI-driven optimization involves leveraging machine learning algorithms to analyze historical data, predict future demand, and optimize procurement decisions in real-time. By crunching vast amounts of data, AI algorithms can identify patterns, detect anomalies, and make accurate forecasts, enabling Purchasing Managers to proactively manage lead time variability and make informed decisions.
One such AI-powered solution is PlanetTogether, a cutting-edge production planning and scheduling software that integrates seamlessly with leading ERP, SCM, and MES systems. Through its advanced algorithms and intuitive interface, PlanetTogether empowers manufacturers to optimize procurement processes, minimize lead time variability, and maximize efficiency across the supply chain.


Integration with ERP, SCM, and MES Systems
The integration between PlanetTogether and industry-leading systems such as SAP, Oracle, Microsoft, Kinaxis, and Aveva unlocks a wealth of benefits for food and beverage manufacturers. By connecting production planning and procurement processes seamlessly, this integration enables real-time data exchange, enhanced visibility, and synchronized operations throughout the organization.
Here's how integration with ERP, SCM, and MES systems enhances procurement optimization:
Real-time Data Synchronization
Integration ensures that data flows seamlessly between different systems, allowing Purchasing Managers to access up-to-date information on inventory levels, production schedules, and supplier performance. Real-time data synchronization enables proactive decision-making, reducing the risk of stockouts and minimizing lead time variability.
Enhanced Visibility and Collaboration
With integrated systems, stakeholders across the organization gain visibility into procurement processes, from demand forecasting to supplier management. Enhanced visibility fosters collaboration between departments, enabling cross-functional teams to work together towards common goals and respond quickly to changes in demand or supply.
Predictive Analytics and Optimization
By combining the power of PlanetTogether's AI-driven algorithms with data from ERP, SCM, and MES systems, manufacturers can harness the full potential of predictive analytics. These analytics enable proactive procurement optimization, allowing Purchasing Managers to anticipate lead time variability, identify potential bottlenecks, and optimize inventory levels accordingly.
Streamlined Procurement Processes
Integration streamlines procurement processes by automating repetitive tasks, eliminating manual errors, and optimizing resource allocation. With seamless connectivity between production planning and procurement systems, manufacturers can achieve greater efficiency, reduce lead times, and improve overall productivity.
AI-driven optimization of procurement lead time variability holds immense potential for food and beverage manufacturers seeking to enhance efficiency, minimize costs, and stay competitive in today's market. By harnessing the power of PlanetTogether integrated with leading ERP, SCM, and MES systems, companies can unlock a new era of procurement excellence, where data-driven decision-making and seamless collaboration drive success.
As a Purchasing Manager, embracing AI-driven solutions and leveraging integration capabilities is key to staying ahead of the curve and achieving operational excellence in procurement. By investing in the right tools and technologies, you can optimize lead time variability, streamline processes, and pave the way for a more efficient and resilient supply chain.
Are you ready to take your manufacturing operations to the next level? Contact us today to learn more about how PlanetTogether can help you achieve your goals and drive success in your industry.