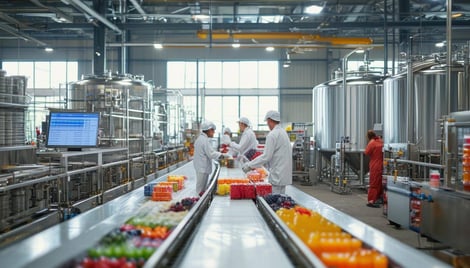
Agility and Flexibility: Transforming Food and Beverage Manufacturing with Advanced Planning Systems
The food and beverage manufacturing industry faces constant change—whether it’s adapting to shifting consumer demands, navigating regulatory pressures, or mitigating supply chain disruptions. In this dynamic environment, production planners play a crucial role in ensuring operational efficiency while maintaining high product quality. The need for agility and flexibility is no longer a luxury; it is a competitive necessity.
Advanced planning systems like PlanetTogether, when integrated with enterprise systems such as SAP, Oracle, Microsoft, Kinaxis, or Aveva, provide a transformative solution for enhancing agility and flexibility in production planning. In this blog, we’ll explore how these integrations empower production planners to stay ahead of challenges while optimizing operational efficiency.
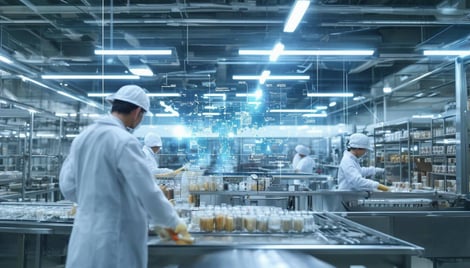
Why Agility and Flexibility Matter
Agility in production planning refers to the ability to respond swiftly to unexpected changes, such as supply chain disruptions or fluctuating consumer preferences. Flexibility, on the other hand, involves having the capacity to adapt processes and workflows without compromising efficiency or quality.
For food and beverage manufacturers, these traits are vital due to:
Seasonal Demand: Peaks and troughs in demand require rapid adjustments to production schedules.
Short Shelf Life: Many products require tight timelines for production, packaging, and distribution.
Regulatory Compliance: Adapting to new regulations often necessitates quick process changes.
Supply Chain Volatility: Ingredient shortages or transportation delays demand immediate re-planning.
Traditional planning methods often fall short in addressing these complexities, creating bottlenecks and inefficiencies. This is where advanced planning systems integrated with ERP solutions can bridge the gap.

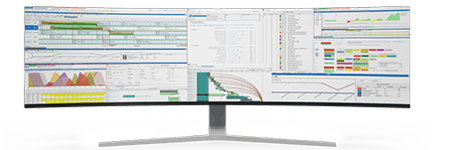
The Role of PlanetTogether in Driving Agility and Flexibility
PlanetTogether is an Advanced Planning and Scheduling (APS) system designed to optimize production workflows. Its integration with leading enterprise solutions like SAP, Oracle, Microsoft Dynamics, Kinaxis, and Aveva enables food and beverage manufacturers to:
Synchronize Data Across Systems: By connecting APS with ERP systems, planners gain real-time visibility into inventory levels, production status, and demand forecasts.
Optimize Schedules Dynamically: PlanetTogether’s algorithms can re-optimize schedules within seconds, ensuring minimal downtime and maximum resource utilization.
Enhance Collaboration: Integrated systems provide a unified platform for stakeholders across production, procurement, and distribution teams, fostering better communication and decision-making.
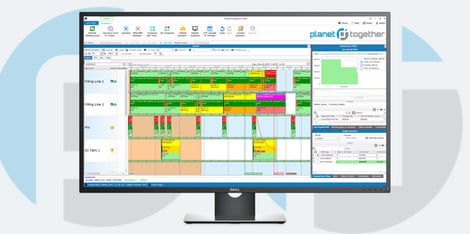
Key Benefits of Integration
1. Real-Time Visibility and Decision Support
With an integrated APS and ERP system, production planners have access to real-time data from across the organization. For example, integrating PlanetTogether with SAP provides insights into:
Current inventory levels
Procurement timelines
Production order statuses
These insights enable planners to make informed decisions, such as prioritizing production runs for high-demand products or reallocating resources to address bottlenecks.
2. Proactive Problem Solving
Agility means being prepared for the unexpected. For instance:
Scenario Planning: Integration with systems like Kinaxis allows planners to simulate different scenarios, such as a sudden ingredient shortage or a surge in demand. PlanetTogether’s scheduling tools can then propose optimal adjustments.
Alerts and Notifications: Integrated systems can provide early warnings for potential issues, enabling planners to take preemptive action.
3. Streamlined Regulatory Compliance
Regulatory compliance is a critical concern for food and beverage manufacturers. By integrating PlanetTogether with Oracle’s ERP solutions, production planners can:
Track and document compliance activities
Quickly adjust schedules to accommodate changes in production processes
Ensure that regulatory requirements are met without disrupting operations
4. Improved Resource Utilization
Flexible scheduling is key to maximizing the use of resources such as labor, machinery, and raw materials. Integration with Microsoft Dynamics enables PlanetTogether to:
Align production schedules with workforce availability
Minimize waste by synchronizing production runs with raw material expiration dates
Ensure equipment is utilized optimally, reducing downtime
5. Enhanced Customer Responsiveness
Consumer demands in the food and beverage sector can shift rapidly. With the combined power of PlanetTogether and Aveva’s manufacturing execution systems (MES), production planners can:
Adjust production schedules to meet urgent orders
Provide accurate delivery timelines to customers
Adapt quickly to changes in order volumes or product specifications
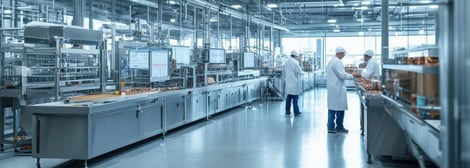
The Future of Agility and Flexibility in Food and Beverage Manufacturing
As consumer demands become more unpredictable and supply chains grow increasingly complex, the importance of agility and flexibility will only continue to rise. Integrating advanced planning systems like PlanetTogether with enterprise solutions such as SAP, Oracle, Microsoft, Kinaxis, or Aveva equips production planners with the tools they need to thrive in this challenging environment.
By leveraging these technologies, food and beverage manufacturers can:
Respond rapidly to changes
Optimize resource utilization
Enhance customer satisfaction
Maintain a competitive edge
In a world where adaptability is key, embracing advanced planning and integration is not just an option—it is the path forward.
Are you ready to take your manufacturing operations to the next level? Contact us today to learn more about how PlanetTogether can help you achieve your goals and drive success in your industry.
LEAVE A COMMENT