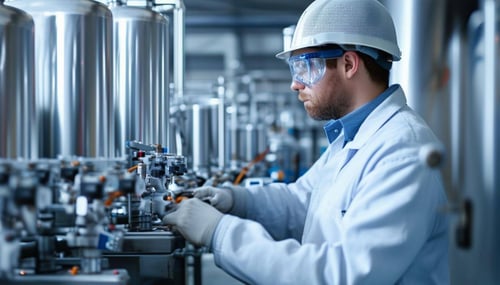
Advanced Process Control: Driving Efficiency in Chemical Manufacturing
The chemical manufacturing industry is at the forefront of innovation, with continuous advancements in process optimization and operational efficiency. As global demand increases and regulatory requirements grow more stringent, Plant Managers must explore new technologies to remain competitive. One such technological evolution is the adoption of Advanced Process Control (APC) technologies.
APC systems provide enhanced monitoring, control, and optimization of chemical manufacturing processes, enabling plants to improve productivity, reduce costs, and maintain product quality. When integrated with advanced planning and scheduling solutions like PlanetTogether and enterprise platforms such as SAP, Oracle, Microsoft Dynamics, Kinaxis, or Aveva, APC technologies become even more powerful.
This blog will look into the role of APC in chemical manufacturing, the benefits of integration, and the steps for successful implementation.
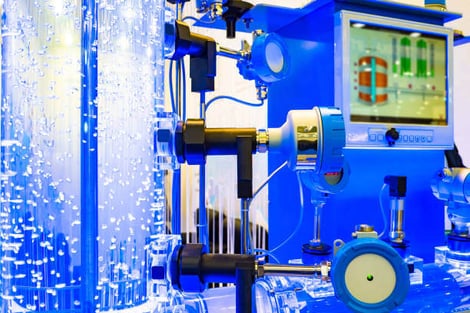
Advanced Process Control in Chemical Manufacturing
Chemical manufacturing processes are inherently complex, involving numerous variables that must be precisely controlled to ensure product consistency and safety. Traditional control systems, like Proportional-Integral-Derivative (PID) controllers, have long been used to manage these variables. However, these systems often struggle with complex, multivariable processes, leading to inefficiencies and variability.
APC technologies, such as Model Predictive Control (MPC), address these challenges by using mathematical models to predict process behavior and make real-time adjustments. Key functionalities of APC include:
Real-Time Optimization: APC continuously adjusts process parameters to maximize efficiency.
Quality Control: It ensures consistent product quality by minimizing variability.
Energy Efficiency: APC reduces energy consumption by optimizing resource utilization.
Predictive Maintenance: It identifies potential equipment failures, reducing downtime.
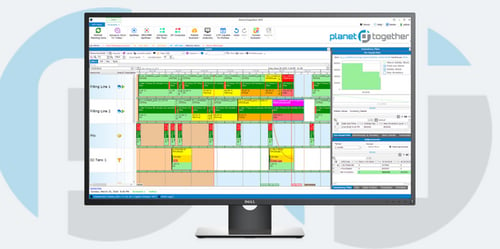
The Benefits of Integrating APC with PlanetTogether and Leading Enterprise Platforms
The true potential of APC technologies is realized when integrated with advanced scheduling and enterprise resource planning (ERP) systems. Platforms like PlanetTogether APS (Advanced Planning and Scheduling) can significantly enhance the value of APC by providing a holistic view of production operations. When paired with ERP systems such as SAP, Oracle, Microsoft Dynamics, Kinaxis, or Aveva, the integration delivers several key benefits:
Improved Production Planning and Scheduling
APC systems generate real-time process data that PlanetTogether APS can utilize to optimize production schedules. By predicting process outcomes, APC helps in anticipating production bottlenecks, adjusting schedules dynamically, and ensuring on-time delivery. Integration with ERP platforms ensures that production plans align with overall business objectives.
Enhanced Process Visibility
Integrating APC with PlanetTogether and ERP systems provides Plant Managers with a unified dashboard to monitor and control operations. Real-time data from the plant floor is correlated with scheduling and inventory information, enabling better decision-making.
Cost Reduction and Energy Savings
APC technologies optimize process parameters to reduce energy consumption and raw material waste. When integrated with ERP systems like SAP, these efficiencies are translated into cost savings that are reflected in financial reports, helping management identify further optimization opportunities.
Increased Flexibility and Scalability
The chemical manufacturing industry often requires rapid adjustments to production schedules due to changing customer demands or regulatory updates. Integration with PlanetTogether and platforms like Kinaxis enhances the plant's ability to respond quickly to these changes without compromising efficiency or product quality.
Regulatory Compliance and Reporting
Chemical manufacturing is subject to stringent environmental and safety regulations. APC systems track process parameters and generate compliance data automatically. When integrated with ERP systems like Aveva, compliance reports can be generated easily, reducing the administrative burden.
Real-World Application: APC and PlanetTogether in Action
Consider a chemical manufacturing facility facing frequent process variability, resulting in production delays and increased energy consumption. The plant implemented an APC system with MPC capabilities to stabilize operations. To maximize the impact, they integrated the APC with PlanetTogether APS and SAP ERP.
The Results:
Production Efficiency: Through real-time adjustments and optimized schedules, the facility increased production output by 15%.
Energy Savings: Energy consumption was reduced by 12%, resulting in substantial cost savings.
Quality Improvement: Product quality consistency improved, leading to fewer reworks.
Compliance: Automated data collection simplified regulatory reporting.
Key Considerations for Successful Integration
While the benefits of APC integration with PlanetTogether and ERP platforms are compelling, successful implementation requires careful planning and execution. Here are key considerations for Plant Managers:
Define Clear Objectives: Identify specific goals, such as reducing energy consumption or improving product quality.
Ensure Data Integrity: APC systems rely on accurate, real-time data. Validate data sources to avoid errors.
Engage Cross-Functional Teams: Involve process engineers, IT teams, and production planners to ensure alignment.
Select the Right Technology Partners: Choose APC and APS solutions compatible with existing ERP platforms.
Invest in Training: Equip staff with the necessary skills to operate and maintain the integrated systems.
Advanced Process Control technologies are revolutionizing chemical manufacturing by delivering unprecedented process optimization and operational efficiency. When integrated with PlanetTogether APS and enterprise platforms like SAP, Oracle, Microsoft Dynamics, Kinaxis, or Aveva, APC systems provide Plant Managers with powerful tools to enhance productivity, reduce costs, and maintain product quality.
Adopting APC and leveraging its integration with advanced planning and enterprise systems will be crucial for maintaining a competitive edge. By investing in these technologies today, chemical manufacturing facilities can build a resilient, efficient, and sustainable future.
Are you ready to take your manufacturing operations to the next level? Contact us today to learn more about how PlanetTogether can help you achieve your goals and drive success in your industry.