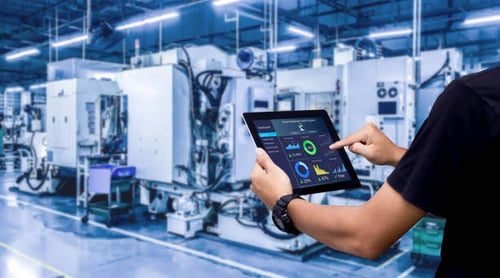
Advanced Data Analytics for Predictive Maintenance in Chemical Manufacturing
In chemical manufacturing, production planners face continuous challenges in ensuring operational efficiency while maintaining compliance and safety. Unexpected equipment failures can lead to costly downtime, waste, and compliance risks. To mitigate these risks, advanced data analytics and predictive maintenance have become critical tools for proactive decision-making.
When integrated with advanced planning and scheduling (APS) solutions like PlanetTogether and enterprise resource planning (ERP) systems such as SAP, Oracle, Microsoft, Kinaxis, or Aveva, predictive maintenance strategies offer an unparalleled advantage in optimizing production schedules and reducing operational disruptions.
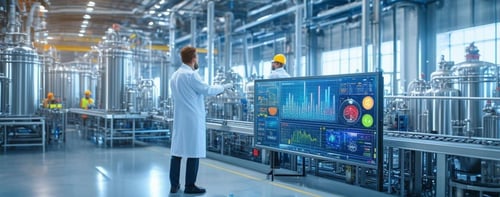
The Role of Predictive Maintenance in Chemical Manufacturing
Traditional maintenance strategies often follow either a reactive or preventive approach. Reactive maintenance results in costly downtime and inefficiencies, while preventive maintenance, though structured, often leads to unnecessary maintenance activities that may not be required. Predictive maintenance, powered by advanced data analytics, AI, and machine learning, provides a middle ground by enabling manufacturers to predict and prevent failures before they occur.
By analyzing real-time and historical data from sensors, machinery logs, and production systems, predictive maintenance solutions can detect anomalies, schedule maintenance at the most opportune times, and extend the lifespan of critical equipment. This enhances overall equipment effectiveness (OEE) and reduces operational risks.
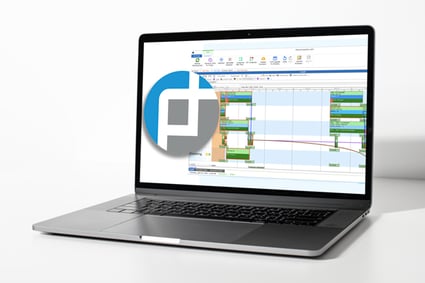
How Advanced Data Analytics Enhances Predictive Maintenance
The success of predictive maintenance depends on data-driven insights generated from various sources across the production floor. Key technologies and methodologies that contribute to its effectiveness include:
IoT and Real-time Sensor Data:
Internet of Things (IoT) sensors collect real-time machine data, measuring parameters such as vibration levels, temperature fluctuations, and pressure changes. These sensors feed into APS systems like PlanetTogether, which then synchronizes maintenance schedules with production planning.
Machine Learning Algorithms:
AI-driven models analyze patterns from past failures and predict when specific equipment is likely to require servicing. This ensures maintenance is performed only when necessary, improving cost efficiency and uptime.
Big Data Analytics:
With SAP, Oracle, Microsoft, Kinaxis, or Aveva ERP solutions, manufacturers can integrate large volumes of structured and unstructured data. Advanced data analytics platforms consolidate data from different sources and provide predictive insights in real time.
Digital Twins for Simulation and Forecasting:
By leveraging Aveva or Microsoft digital twin technology, manufacturers can create virtual models of production environments, testing various maintenance scenarios to identify the optimal approach before taking any physical action.
Cloud-based Integration for Seamless Data Flow:
Cloud-based platforms facilitate real-time data exchange between PlanetTogether APS and ERP systems, ensuring that production schedules automatically adjust based on maintenance predictions without manual intervention.
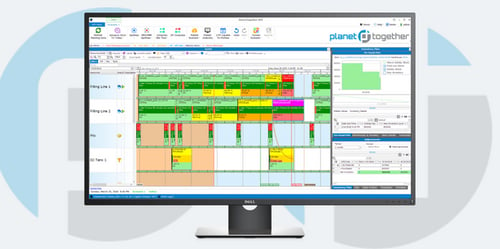
Integrating Predictive Maintenance with APS and ERP Systems
To maximize the benefits of predictive maintenance, integration with APS and ERP systems is essential. This ensures that production planning remains agile, efficient, and resilient to potential disruptions. Here’s how the integration works:
Data Collection & Processing:
Sensors and IoT devices collect operational data, which is processed using AI-powered analytics engines integrated into ERP systems like SAP, Oracle, Kinaxis, or Microsoft Dynamics.
Predictive Insights & Alerts:
Predictive models identify patterns and forecast potential equipment failures. Alerts are sent to production planners via APS platforms like PlanetTogether, enabling them to adjust production schedules accordingly.
Automated Scheduling Adjustments:
When a machine is predicted to require maintenance, PlanetTogether APS automatically reschedules production runs to minimize downtime while ensuring resource optimization.
Supply Chain Alignment:
Integration with SAP, Oracle, or Kinaxis supply chain solutions ensures that raw materials, spare parts, and workforce availability align with the predictive maintenance schedule.
Advanced data analytics for predictive maintenance is revolutionizing the way chemical manufacturers approach production planning. By integrating PlanetTogether APS with leading ERP systems like SAP, Oracle, Microsoft, Kinaxis, and Aveva, production planners can achieve new levels of efficiency, reliability, and cost-effectiveness. Investing in predictive maintenance is no longer a luxury but a necessity for staying competitive in an increasingly digitalized and automated manufacturing landscape.
With the right integration strategy, production planners can not only enhance equipment reliability but also optimize scheduling, improve compliance, and drive sustainable operations in chemical manufacturing. As predictive analytics continues to evolve, organizations that embrace data-driven predictive maintenance will set the benchmark for efficiency, safety, and profitability in the industry.
Are you ready to take your manufacturing operations to the next level? Contact us today to learn more about how PlanetTogether can help you achieve your goals and drive success in your industry.
LEAVE A COMMENT