Adopting Automation for Repetitive Tasks
As consumer demands fluctuate, margins tighten, and compliance requirements evolve, the ability to streamline repetitive tasks through automation becomes a strategic priority. For Manufacturing IT Managers in food and beverage facilities, adopting automation technologies—particularly by integrating specialized software solutions like PlanetTogether with enterprise systems like SAP, Oracle, Microsoft, Kinaxis, or Aveva—opens pathways to increased efficiency, reduced costs, and improved accuracy across routine workflows.
In this blog, we’ll explore how automation for repetitive tasks is transforming the food and beverage industry, highlight specific opportunities for IT managers, and discuss the benefits of integrating automation solutions with established enterprise software systems.
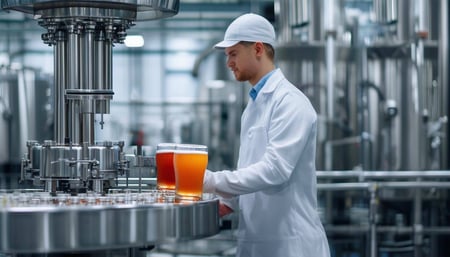
The Case for Automation in Food and Beverage Manufacturing
Repetitive tasks in food and beverage manufacturing—such as production scheduling, inventory management, quality checks, and compliance tracking—often consume significant time and resources when managed manually. These processes are also prone to errors, which can impact product quality and lead to costly compliance issues. Automating such tasks can address these challenges by:
Reducing manual intervention: Automation decreases reliance on human input for routine tasks, freeing up staff for more strategic roles.
Increasing accuracy: Automated systems reduce human error, ensuring consistent quality and compliance with food safety standards.
Enhancing traceability: Automation systems can quickly log and track information, making it easier to trace ingredients and finished products through the supply chain.
Improving response times: Automated processes allow for real-time responses to operational issues, minimizing production downtime and reducing lead times.
For IT managers, the challenge lies in identifying which tasks can be automated and understanding how best to implement these technologies with minimal disruption to current operations.
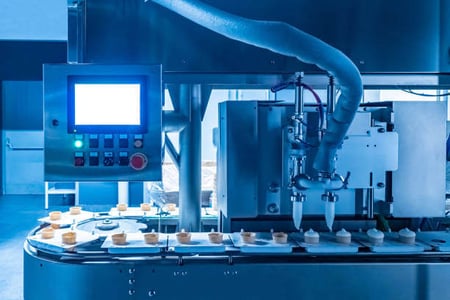
Key Repetitive Tasks Ideal for Automation in Food and Beverage Facilities
While the potential for automation is vast, here are some of the most impactful areas to consider automating:
Production Scheduling: By integrating scheduling software such as PlanetTogether with ERP systems like SAP or Microsoft Dynamics, you can create automated schedules based on real-time data. This integration can account for variables like equipment availability, production demands, and workforce capacity, ensuring that production schedules remain optimized and adaptable.
Inventory Management: Automating inventory tracking through systems like Oracle and Kinaxis allows for real-time updates on ingredient levels, expiration dates, and reordering needs. Automated inventory monitoring helps prevent stockouts or excess inventory, reducing waste and ensuring smooth production cycles.
Quality Control: Automating quality checks—such as capturing data from sensors and comparing them to predefined standards—can significantly reduce error rates in quality assessments. With an integrated system, real-time quality data can sync with compliance tracking modules in systems like Aveva, simplifying regulatory reporting and traceability.
Maintenance Scheduling: Integrating predictive maintenance solutions with an automation platform like PlanetTogether and SAP’s EAM (Enterprise Asset Management) module allows maintenance schedules to adapt based on real-time machine performance data, minimizing unplanned downtime and extending equipment life.
Order Processing and Fulfillment: Automated order processing, enabled through integrations with ERP systems, helps manufacturers respond to demand fluctuations without bottlenecks, optimizing fulfillment cycles and improving customer satisfaction.

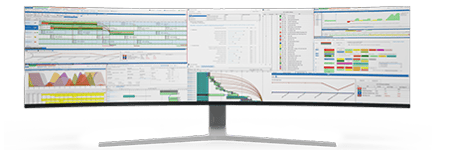
Leveraging PlanetTogether and ERP Integration for Effective Automation
To implement automation effectively, integrating PlanetTogether with enterprise platforms like SAP, Oracle, Microsoft, Kinaxis, or Aveva can play a pivotal role. Such integrations offer a unified platform where data flows seamlessly across systems, enabling automated workflows without the need for constant manual oversight.
Benefits of Integrating PlanetTogether with ERP Systems
Centralized Data Management: Integration ensures that all data—such as inventory levels, production schedules, and order statuses—are synchronized across systems, reducing data silos and providing a holistic view of operations.
Enhanced Decision-Making: Real-time data exchange between PlanetTogether and ERP systems supports more accurate decision-making. For example, if inventory levels dip below a threshold in the ERP system, PlanetTogether can adjust the production schedule accordingly, ensuring seamless operations.
Scalability: As production demands grow, automation solutions integrated with ERP systems can scale accordingly, allowing IT managers to add automated workflows without reengineering entire processes.
Improved Reporting and Compliance: Integrated systems automatically log critical data points, streamlining the reporting process for compliance audits and making it easier to adhere to food safety regulations.
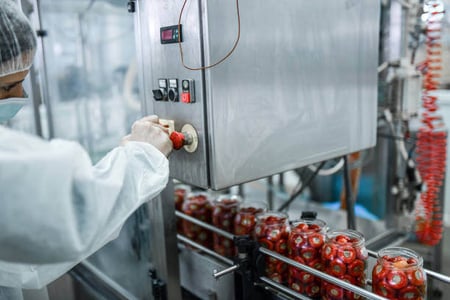
Implementing Automation for Repetitive Tasks: A Practical Roadmap
The transition to automation requires a thoughtful approach to minimize operational disruptions. Here’s a step-by-step roadmap for Manufacturing IT Managers in food and beverage facilities:
Step 1: Identify Automation Opportunities
Begin by assessing which repetitive tasks consume the most time and resources.
Prioritize tasks that involve data processing, inventory management, scheduling, and compliance checks.
Step 2: Evaluate Technology and Integration Options
Select automation tools and platforms that can integrate with your facility’s current ERP system.
Consider PlanetTogether for production scheduling and operations optimization, especially if your facility already relies on SAP, Oracle, Microsoft, Kinaxis, or Aveva.
Step 3: Plan for Data Migration and Integration
Collaborate with ERP and PlanetTogether specialists to ensure a smooth integration, including data migration and system configuration.
Create a unified data structure that allows information to flow between systems, avoiding data silos and minimizing manual data entry.
Step 4: Implement Automation Incrementally
Roll out automation in stages, starting with the highest-priority tasks identified in Step 1.
For each task, monitor outcomes to ensure that automation is delivering the expected benefits, such as time savings and error reduction.
Step 5: Train Employees on New Workflows
Educate your workforce on how automation will change workflows, and provide training on new tools and interfaces.
Emphasize that automation frees up time for higher-value tasks, helping to reduce concerns about job displacement.
Step 6: Monitor and Optimize
Continuously monitor the performance of automated processes, gathering data on efficiency gains, cost savings, and production throughput.
Adjust automation parameters as needed to improve outcomes, especially during demand fluctuations or regulatory changes.
The Benefits of Automation for IT Managers in Food and Beverage Facilities
For IT managers, automating repetitive tasks is about more than simply replacing manual labor—it’s about positioning the facility for future growth, resilience, and efficiency. Some key benefits include:
Enhanced Resource Allocation: With automation handling repetitive tasks, IT staff can focus on more complex, strategic initiatives, such as enhancing cybersecurity, refining data analytics, and exploring AI applications.
Reduced Operational Costs: Automating tasks reduces the labor required for manual processes, potentially decreasing operational costs and enabling more competitive pricing strategies.
Improved Data Accuracy and Compliance: Automated systems capture data at each step, improving traceability and compliance with food safety regulations. Integration with ERP systems ensures that all data is consistently available for audits and quality assessments.
Future-Proofing Through Scalability: Automated workflows can scale with your operation. By implementing an integrated system, you can automate more processes as the facility grows, maintaining efficiency even as production volumes increase.
As technology advances, automation will continue to play a critical role in the food and beverage industry. IT managers will have more tools at their disposal to streamline operations and manage increasing complexities. Technologies like machine learning, IoT, and AI will enhance the capabilities of automation, allowing systems to make real-time adjustments based on predictive insights.
By proactively adopting automation for repetitive tasks today, you’re not only improving current operations but also setting up your facility for a resilient, tech-driven future. Integration with platforms like PlanetTogether and ERP systems like SAP, Oracle, Microsoft, Kinaxis, or Aveva will allow your facility to remain agile, competitive, and responsive to industry changes—positioning it for long-term success in the evolving food and beverage market.
In conclusion, automation for repetitive tasks isn’t just a trend; it’s a vital component of modern food and beverage manufacturing. With the right approach to automation and integration, IT managers can unlock new levels of efficiency, accuracy, and agility—transforming repetitive tasks into seamless workflows that contribute to overall operational excellence.
Are you ready to take your manufacturing operations to the next level? Contact us today to learn more about how PlanetTogether can help you achieve your goals and drive success in your industry.