Adaptive Job Sequencing in Process Manufacturing
In process manufacturing, where every minute and every resource counts, the role of a Production Scheduler is pivotal. The efficient sequencing of jobs directly impacts productivity, resource utilization, and ultimately, the bottom line of a food and beverage manufacturing facility.
In this blog, we look into the concept of adaptive job sequencing and explore how integrating advanced scheduling software like PlanetTogether with ERP systems such as SAP, Oracle, Microsoft, Kinaxis, or Aveva can revolutionize production scheduling.
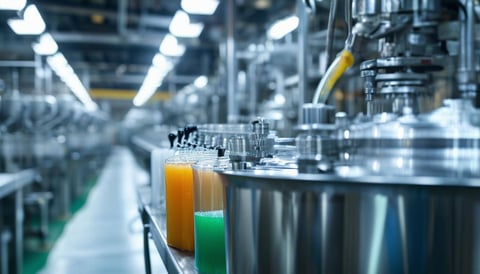
Adaptive Job Sequencing
Job sequencing in manufacturing refers to the process of determining the order in which jobs (production orders or tasks) should be executed on the production floor. In process manufacturing, where products undergo various stages of transformation, job sequencing becomes even more critical due to complex recipe formulations, batch processing, and regulatory compliance requirements.
Traditionally, job sequencing was based on static rules or priorities defined by planners or schedulers. However, in today's fast-paced manufacturing environment, where demand variability, supply chain disruptions, and resource constraints are common, static scheduling approaches often fall short. This is where adaptive job sequencing comes into play.
Adaptive job sequencing involves the dynamic adjustment of job priorities and sequences based on real-time factors such as:
Demand Changes: Immediate shifts in customer orders or market demands.
Resource Availability: Availability of materials, equipment, and labor.
Production Constraints: Operational constraints and regulatory requirements.
Optimization Goals: Minimizing makespan, reducing changeover times, or maximizing resource utilization.
The goal is to optimize production schedules in real-time or near real-time, ensuring that the plan remains responsive and aligned with the latest conditions on the ground.
Challenges in Job Sequencing
Process manufacturing poses unique challenges to job sequencing due to:
Recipe and Formula Management: Handling recipes with multiple ingredients and complex formulations.
Batch Processing: Optimizing batch sizes and sequences to minimize waste and maximize throughput.
Regulatory Compliance: Adhering to strict regulatory requirements for safety, quality, and environmental standards.
These challenges necessitate a sophisticated approach to job sequencing that goes beyond simple prioritization based on due dates or batch sizes.

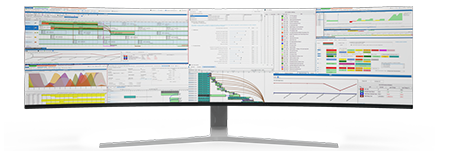
Integration of PlanetTogether with ERP Systems
To tackle these challenges effectively, many food and beverage manufacturers are turning to advanced production scheduling solutions like PlanetTogether, which offer robust capabilities for adaptive job sequencing. Integrating such software with ERP systems such as SAP, Oracle, Microsoft Dynamics, Kinaxis RapidResponse, or Aveva MES can unlock significant benefits:
Real-Time Data Synchronization
Seamless integration allows for real-time updates between production scheduling and ERP modules, ensuring that schedules are based on the latest demand forecasts, inventory levels, and resource capacities.
Enhanced Visibility and Collaboration
Production schedulers gain comprehensive visibility into inventory availability, production capacities, and order statuses across the supply chain. This visibility enables better decision-making and facilitates collaboration with other departments.
Scenario Planning and What-If Analysis
Advanced scheduling software combined with ERP integration supports scenario planning and what-if analysis. Production schedulers can simulate different production scenarios, evaluate the impact of potential changes, and choose the optimal schedule that meets operational goals.
Automated Schedule Adjustments
By leveraging real-time data and advanced algorithms, integrated systems can automatically adjust schedules in response to unforeseen events such as machine breakdowns, material shortages, or rush orders. This agility helps minimize disruptions and maintain production efficiency.
Compliance and Traceability
Integrated systems ensure that production schedules adhere to regulatory requirements, including batch traceability and compliance with food safety standards. Automated record-keeping and reporting simplify audits and regulatory inspections.
Best Practices for Implementation
Implementing adaptive job sequencing through integration requires careful planning and execution:
Define Clear Objectives:
Align scheduling objectives with business goals such as cost reduction, improved customer service, or enhanced operational efficiency.
Engage Stakeholders:
Involve production teams, IT specialists, and senior management in the implementation process to ensure alignment with organizational strategies.
Training and Support:
Provide comprehensive training to production schedulers and other users on the new scheduling software and integrated ERP functionalities.
Continuous Improvement:
Monitor key performance indicators (KPIs) post-implementation and continuously refine scheduling strategies based on feedback and insights.
Adaptive job sequencing in process manufacturing is not just a concept but a critical strategy for achieving operational excellence. By integrating advanced scheduling solutions like PlanetTogether with leading ERP systems, food and beverage manufacturers can streamline production scheduling, enhance agility, and optimize resource utilization.
Production schedulers play a central role in driving these improvements, leveraging real-time data and advanced algorithms to make informed decisions that impact overall efficiency and competitiveness.
The role of adaptive job sequencing will become even more integral in meeting the demands of a rapidly changing marketplace. Embracing integration between PlanetTogether and ERP systems is not just a step forward—it's a leap towards a smarter, more responsive manufacturing future.
Are you ready to take your manufacturing operations to the next level? Contact us today to learn more about how PlanetTogether can help you achieve your goals and drive success in your industry.