Operational Excellence with Synchronized Manufacturing Systems
Chemical manufacturing facilities are under increasing pressure to optimize their production processes while ensuring efficiency, quality, and compliance. Production schedulers play a pivotal role in this endeavor, tasked with orchestrating the intricate dance of production schedules, resources, and customer demands. However, the traditional approach of relying solely on manual scheduling methods or disparate systems can lead to inefficiencies, bottlenecks, and missed opportunities.
Enter synchronized manufacturing systems – a fundamental change in the way chemical manufacturing facilities approach production scheduling and management.
By integrating advanced scheduling software like PlanetTogether with leading Enterprise Resource Planning (ERP), Supply Chain Management (SCM), and Manufacturing Execution Systems (MES) such as SAP, Oracle, Microsoft, Kinaxis, Aveva, and others, production schedulers can unlock a new level of operational excellence.
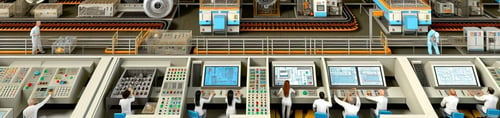
The Case for Integration
In today's interconnected world, siloed systems are no longer sufficient to meet the demands of modern manufacturing. The integration of scheduling software with ERP, SCM, and MES systems offers several compelling advantages:
Real-time Visibility: Integration provides production schedulers with real-time visibility into the entire manufacturing process, from raw materials procurement to finished product delivery. This visibility enables proactive decision-making, allowing schedulers to anticipate and mitigate potential issues before they escalate.
Streamlined Processes: By synchronizing scheduling with ERP, SCM, and MES systems, manual data entry and duplication are eliminated. This streamlines processes, reduces errors, and ensures that everyone in the organization is working from the same data, fostering alignment and collaboration across departments.
Optimized Resource Utilization: Integrated systems enable production schedulers to optimize resource utilization by aligning production schedules with available capacity, inventory levels, and workforce availability. This optimization minimizes downtime, maximizes throughput, and reduces costs, ultimately improving the bottom line.
Agility and Flexibility: In today's volatile market conditions, agility and flexibility are essential for survival. Synchronized manufacturing systems empower production schedulers to quickly adjust schedules in response to changing customer demands, market dynamics, or unexpected disruptions, ensuring that the organization remains responsive and resilient.

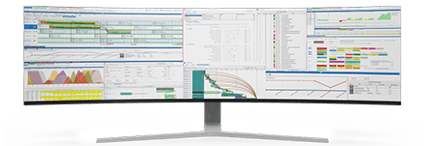
The Power of PlanetTogether Integration
At the heart of synchronized manufacturing systems lies advanced scheduling software like PlanetTogether. PlanetTogether offers a robust set of features designed to optimize production scheduling, including:
Finite Capacity Scheduling: PlanetTogether's finite capacity scheduling capabilities allow production schedulers to account for resource constraints, such as equipment availability, labor constraints, and material shortages, when creating production schedules. This ensures that schedules are realistic and achievable, minimizing the risk of overcommitment and bottlenecks.
What-If Analysis: PlanetTogether enables production schedulers to perform what-if analysis to evaluate the impact of different scenarios on production schedules. This capability allows schedulers to assess the feasibility of proposed changes or identify potential risks before implementing them, enabling informed decision-making and risk management.
Seamless Integration: PlanetTogether seamlessly integrates with leading ERP, SCM, and MES systems, including SAP, Oracle, Microsoft, Kinaxis, Aveva, and others. This integration enables bi-directional data exchange, ensuring that scheduling decisions are based on the most up-to-date information available across the organization.
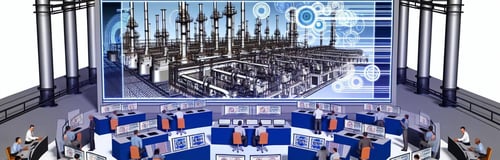
Best Practices for Implementing Synchronized Manufacturing Systems
While the benefits of synchronized manufacturing systems are clear, successful implementation requires careful planning and execution. Here are some best practices to consider:
Define Clear Objectives: Clearly define the objectives and goals of the integration initiative, such as improving on-time delivery, reducing lead times, or increasing resource utilization. This will guide the implementation process and help measure success.
Engage Stakeholders: Involve key stakeholders from across the organization, including production, operations, IT, and management, in the implementation process. Their input and buy-in are essential for successful integration and adoption.
Data Quality and Standardization: Ensure that data quality and standardization practices are in place across systems to facilitate seamless integration and accurate decision-making. This may involve cleansing and harmonizing data, establishing data governance policies, and implementing data validation checks.
Training and Change Management: Provide comprehensive training and support to production schedulers and other users to ensure they are proficient in using the integrated systems. Additionally, implement change management strategies to address any resistance or concerns and foster a culture of continuous improvement.
Monitor and Measure Performance: Continuously monitor and measure key performance indicators (KPIs) to gauge the impact of synchronized manufacturing systems on operational efficiency, customer satisfaction, and financial performance. Use this data to identify areas for improvement and optimize processes further.
Synchronized manufacturing systems represent a fundamental change in the way chemical manufacturing facilities approach production scheduling and management. By integrating advanced scheduling software like PlanetTogether with leading ERP, SCM, and MES systems, production schedulers can unlock a new level of operational excellence, driving efficiency, agility, and competitiveness.
However, successful implementation requires careful planning, stakeholder engagement, and a commitment to continuous improvement. By following best practices and leveraging the power of integrated systems, chemical manufacturing facilities can optimize their production processes, meet customer demands, and thrive in today's dynamic market landscape.
Are you ready to take your manufacturing operations to the next level? Contact us today to learn more about how PlanetTogether can help you achieve your goals and drive success in your industry.