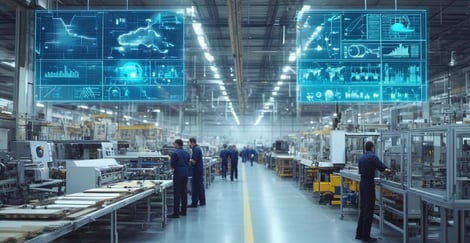
8 Scheduling Strategies to Enhance Throughput in Bottleneck Areas
In industrial manufacturing facilities, bottlenecks are inevitable. They can occur at any stage of the production process, from the initial assembly line to the final stages of packaging. Bottlenecks constrain throughput, disrupt schedules, and increase lead times. For production schedulers, the challenge is not just identifying these constraints but also implementing strategies to alleviate them effectively.
The integration of advanced scheduling tools like PlanetTogether with enterprise systems such as SAP, Oracle, Microsoft, Kinaxis, or Aveva has revolutionized how production facilities manage bottlenecks. These integrations provide real-time visibility, actionable insights, and automated solutions to optimize production schedules.

This blog explores key scheduling strategies to enhance throughput in bottleneck areas, emphasizing the role of advanced integrations.
1. Identify and Monitor Bottlenecks
Before addressing bottlenecks, you need to identify them. Common indicators include:
Accumulation of work-in-progress (WIP): Stations upstream of the bottleneck often have excess inventory.
Idle downstream processes: Machines or workers waiting for inputs from the bottlenecked area.
Extended cycle times: A noticeable slowdown in overall production.
By integrating PlanetTogether with SAP or Oracle, schedulers can access real-time data on production performance. For example, SAP’s manufacturing execution systems (MES) can feed machine-level data into PlanetTogether, enabling schedulers to pinpoint bottlenecks with precision. This real-time synchronization eliminates the delays associated with manual data collection and analysis.
2. Prioritize Production Based on Bottlenecks
Once bottlenecks are identified, prioritizing their workload is critical. Strategies include:
Sequencing high-priority jobs: Ensure that critical orders pass through the bottleneck first.
Minimizing setup times: Group similar jobs to reduce changeover delays.
Balancing workloads: Redistribute tasks from overloaded machines to underutilized ones.
PlanetTogether’s scheduling algorithms, when integrated with Microsoft Dynamics, allow schedulers to simulate various scenarios and determine the best approach to prioritize jobs. This proactive planning minimizes downtime and ensures optimal use of constrained resources.
3. Implement Drum-Buffer-Rope (DBR) Scheduling
Drum-Buffer-Rope is a proven methodology for managing bottlenecks:
Drum: The bottleneck sets the pace for production.
Buffer: Create a time or inventory buffer before the bottleneck to ensure it always has work.
Rope: Coordinate the flow of materials to ensure upstream processes don’t overload the bottleneck.
When integrated with Aveva’s operational tools, PlanetTogether can dynamically adjust the DBR parameters in response to changing production conditions. For example, if an unexpected machine breakdown occurs, the system can reallocate resources and update buffers automatically, maintaining a steady flow through the bottleneck.
4. Use Finite Scheduling for Realistic Plans
Finite scheduling ensures that production plans consider the actual capacity constraints of bottlenecks. Unlike infinite scheduling, which assumes unlimited resources, finite scheduling produces realistic, actionable schedules.
With PlanetTogether’s integration with Kinaxis, production schedulers can leverage finite scheduling capabilities to create feasible plans that align with real-world limitations. Kinaxis’ demand and supply planning insights feed directly into PlanetTogether, ensuring that schedules are not only realistic but also optimized for current demand.
5. Leverage Predictive Analytics
Modern manufacturing facilities generate vast amounts of data, much of which can be used to predict potential bottlenecks. Predictive analytics can forecast machine failures, staffing shortages, or material delays that might exacerbate bottlenecks.
By integrating PlanetTogether with Oracle’s cloud analytics, schedulers can harness predictive capabilities to anticipate and prevent bottlenecks. For instance, if analytics predict a high likelihood of equipment failure in a critical bottleneck, schedulers can preemptively adjust production schedules or allocate maintenance resources.
6. Optimize Resource Utilization
Maximizing throughput at bottleneck areas often requires reallocating resources. Strategies include:
Cross-training staff: Ensuring workers can operate multiple machines reduces downtime during transitions.
Reassigning tasks: Shifting non-bottleneck tasks away from critical areas to free up capacity.
PlanetTogether’s integration with Microsoft Power BI allows for detailed resource utilization reports. These insights help schedulers make informed decisions about where to allocate workers, materials, and equipment for maximum efficiency.
7. Implement Real-Time Adjustments
Static schedules are rarely sufficient in dynamic manufacturing environments. Real-time adjustments are essential to adapt to unexpected changes, such as rush orders, equipment breakdowns, or material shortages.
PlanetTogether’s integration with SAP provides real-time visibility into production processes. If a bottleneck arises, schedulers can use SAP’s advanced planning and optimization tools to make immediate adjustments, ensuring minimal disruption.
8. Focus on Continuous Improvement
Addressing bottlenecks is not a one-time task. Continuous monitoring and improvement are necessary to sustain high throughput. Key practices include:
Regular audits: Analyze production data to identify emerging bottlenecks.
Feedback loops: Use operator feedback to refine scheduling strategies.
Invest in upgrades: Consider equipment or technology investments to alleviate chronic bottlenecks.
Integrations between PlanetTogether and Aveva enable a closed-loop approach to continuous improvement. Aveva’s operational insights feed into PlanetTogether, creating a cycle of data-driven optimization.
Enhancing throughput in bottleneck areas is a complex but achievable goal. With advanced scheduling tools like PlanetTogether and their integration with enterprise systems such as SAP, Oracle, Microsoft, Kinaxis, or Aveva, production schedulers can implement data-driven strategies that optimize bottlenecks and improve overall efficiency.
From prioritizing production and leveraging predictive analytics to adopting methodologies like Drum-Buffer-Rope and finite scheduling, the right strategies can transform bottlenecks from constraints into opportunities for growth.
For production schedulers in industrial manufacturing, these tools and strategies represent not just a way to manage challenges but a path to sustained operational excellence.
Are you ready to take your manufacturing operations to the next level? Contact us today to learn more about how PlanetTogether can help you achieve your goals and drive success in your industry.