2020 is definitely an interesting time for supply chain and manufacturing. As the economy has been on the rise for the last few years, we are finally finding ourselves slowing down and even coming to a dead stop within the last month.
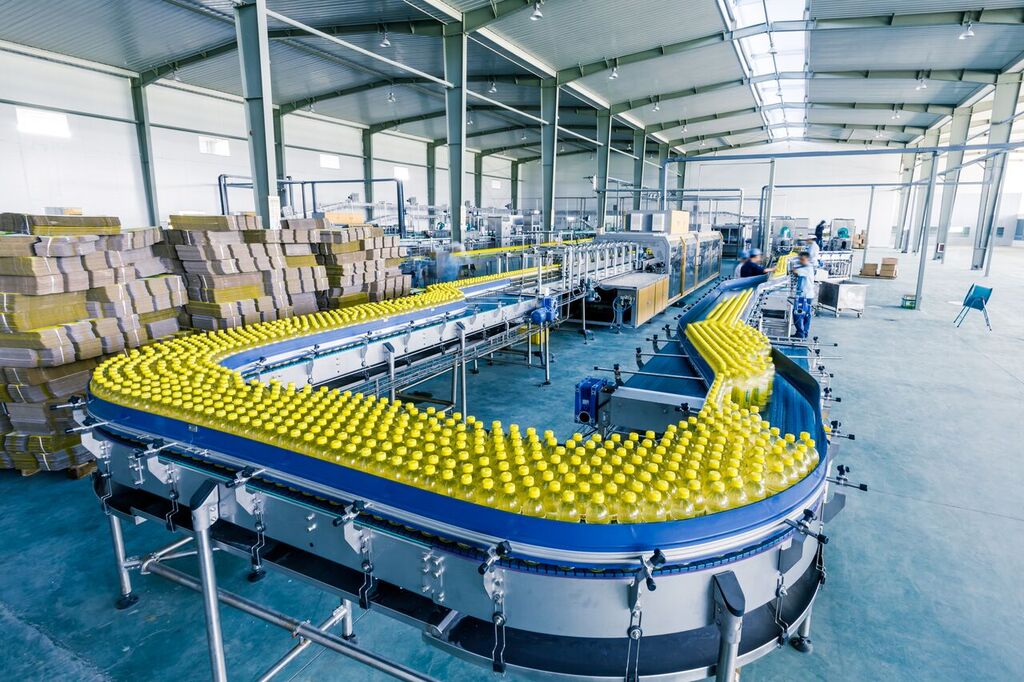
With a slowing global economy, volatile trade agreements, and ongoing labor shortages, manufacturing is facing a great deal of challenges for this following year - especially with the novel coronavirus making waves across the world. This is why keeping up with manufacturing trends in 2020 is an absolute necessity and may aid your manufacturing with coming up with a plan for the following months that are ahead. Therefore, within this blog, we are going to discuss the 5 manufacturing trends to watch in 2020.
5 Manufacturing Trends to Watch in 2020
The five trends to watch in manufacturing in 2020 pertain to the following:
- Digital Transformation - Digital transformation is critical to your supply chain and ensures that you remain relevant and competitive within your industry. Success requires the acceptance of digital transformation - you don’t want to get lost in the past. This include enabling adoption and assessing ROIs of utilizing technology that can aid with your supply chain and production process. While there are challenges, such as acquainting yourself with new technology and educating your employees, following through with digital transformation will ensure that you stay ahead of the curve.
- Headwinds for Supply Chains/Logistics - In spite of a challenging trade and tariff environment, revenues and earnings will need to remain strong for middle market companies, with domestically focused industrial companies experiencing greater growth than those that sell on global markets. Many companies have enforced changes in global supply chains and have started to look more thorough into producing in countries such as Mexico and the United States. This has definitely become a main trend and topic due to the coronavirus outbreak within the last several months.
- Technology/Workforce Future - Innovation is driving profound change on the factory floor as mechanical and electrical processes are increasingly being managed through sensors and robotics. In correlation with digital transformation, keeping up with the rapidly changing technological factors of manufacturing are key when attempting to improve efficiency within your operation. The downside of implementation would be the need for a flexible and skilled workforce. This would put workers at risk as well, with many jobs being lost to automation, especially those of low-skilled and low-wage workers. Therefore, keeping up with the technology and workforce future is by far one of the most important aspects pertaining to the future of supply chain.
- Slowing Global Trade - As global economic growth has soared over the last few years, we are finally beginning to slow down, even coming to a halt now with the coronavirus. Tariffs are also affecting business results and have hindered some companies that operate globally. Slowing global trade was a primary concern even before the coronavirus came into play, now we know that it is certain. Pay attention to the economic factors pertaining to the virus and what trade/manufacturing will look like in the oncoming months.
- Coronavirus - The coronavirus is by far the largest concern for supply chain in the early months of 2020. With an uncertain outcome, many manufacturers find that it is unclear where this is going to lead us. Keeping an eye on the quickly changing situation of the coronavirus and how to efficiently improve your operation to ensure that you are keeping costs low and ultimately meeting a quickly changing demand is a must. With many manufacturers not having experienced this in the past, this is by far one of the most critical and crucial times for figuring out a plan for your supply chain and the future of your company.
Understanding and keeping up with the manufacturing trends of 2020 is absolutely essential in understanding where the supply chain industry is heading in the following months. With challenges such as the coronavirus and slowing global trade being a huge factor in our economy as of right now, manufacturers are finding themselves looking for softwares that can aid with demand planning, inventory management, and ultimately a way to improve their operation during this time period. A software that can greatly aid with this concept is PlanetTogether’s Advanced Planning and Scheduling (APS) Software. Advanced Planning and Scheduling (APS) Software can ensure for thorough visibility into your manufacturing operation and locate areas that are in need of efficiency enhancement in order to cut costs within an operation. Overall, PlanetTogether’s Advanced Planning and Scheduling (APS) Software is becoming a vital component pertaining to supply chain’s around the globe.
Advanced Planning and Scheduling Software
Advanced Planning and Scheduling (APS) software has become a must for modern-day manufacturing operations due to customer demand for increased product mix and fast delivery combined with downward cost pressures. APS can be quickly integrated with a ERP/MRP software to fill gaps where these system lack planning and scheduling flexibility and accuracy. Advanced Planning and Scheduling (APS) helps planners save time while providing greater agility in updating ever-changing priorities, production schedules, and inventory plans.
- Create optimized schedules balancing production efficiency and delivery performance
- Maximize output on bottleneck resources to increase revenue
- Synchronize supply with demand to reduce inventories
- Provide company-wide visibility to capacity
- Enable scenario data-driven decision making
Implementation of Advanced Planning and Scheduling (APS) software will take your manufacturing operations to the next level of production efficiency, taking advantage of the operational data you already have in your ERP.
Related Multi PlantVideo
APS Resources